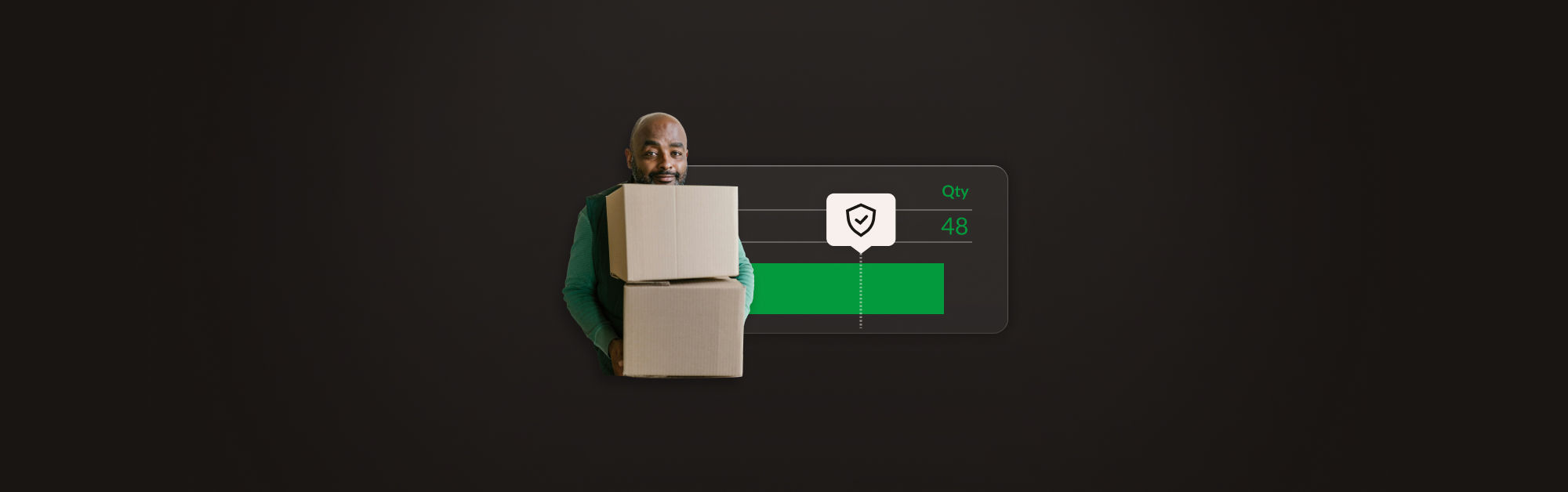
Safety stock acts as a buffer against the unexpected. Whether it’s a surge in demand, supply chain delays or forecasting errors, it’s how you keep shelves stocked when things don’t go according to plan. For businesses on the rise, it protects both revenue and reputation.
Keeping safety stock minimizes the chance of stockouts and the costly scramble to restock. It keeps operations steady and ensures customers leave satisfied. If you’re managing multiple locations, it also helps maintain a consistent experience across your stores.
A smart safety stock approach not only prevents stockouts but also keeps your inventory agile and profits steady.
- Why is safety stock important?
- How to calculate safety stock
- Factors to consider when determining safety stock levels
- Benefits of maintaining safety stock
- Challenges of safety stock management
Grow your retail business.
Streamline inventory, suppliers, teams and stores with Lightspeed's all-in-one platform. From intuitive POS and stock management features to powerful reporting, Lightspeed gives you the tools you need to grow.
Why is safety stock important?
Prevents stockouts
The effects of a stockout can lead to a ripple effect of lost sales, frustrated customers and even operational slowdowns. But having safety stock on hand can prevent these unpleasant issues by ensuring essential items are available even during demand spikes or shipping delays. With the right safety stock formula in place, your business stays ready to meet demand and keep operations running smoothly.
Buffers against uncertainty
Supply chains are unpredictable; delayed shipments, supplier hiccups or sudden demand changes can throw off your operations. Planning for safety stock inventory absorbs these shocks, covering unexpected spikes or seasonal demand shifts. It also keeps you covered during supply disruptions like late deliveries or product defects.
Maintains consistent operations
Consistency is the name of the game for businesses managing multiple locations. Safety stock helps keep inventory flowing across all locations, ensuring smooth operations without delays. It acts as a safeguard against disruptions, helping both retailers and manufacturers maintain steady operations, protect revenue and deliver a more reliable customer experience.
Protects against forecasting errors
No forecast is perfect. Market shifts or unforeseen challenges can leave even the most accurate predictions off target. Safety stock helps close that gap, protecting your business from running out of key items. It also shields you from unreliable suppliers, so your operations don’t suffer from missed deliveries or delays.
Think of safety stock as more than just extra inventory; it’s a strategic safeguard that keeps your business running smoothly no matter what comes your way.
How to calculate safety stock
Knowing how to balance the unpredictability of demand spikes, lead time delays and service levels can be the key to managing your safety stock effectively. The right approach depends on your business model, inventory flow and supply chain complexity. Let’s explore some of the most common methods to help you find the best fit.
Basic safety stock formula
This is the simplest way to calculate safety stock. It focuses on your maximum usage and lead time:
Think of it as a shield against worst-case scenarios. Let’s say your store typically sells 30 units per day, but during a peak period, sales jump to 50 units. If your lead time is 10 days, you’d hold 500 units as safety stock to avoid running out during those high-demand days.
Statistical methods
This method adds a layer of precision by factoring in variability and risk. The safety stock formula may look complicated, but don’t fret!
Here’s how it works: Z is your service level (e.g., 95% or 99%), σLT is the lead time’s standard deviation and Davg is your average demand. For example, if you sell 100 units daily, lead time varies by 3 days and you aim for a 95% service level (Z = 1.65), your safety stock would be 495 units. This approach works well when you’re balancing both demand and lead time uncertainty.
Advanced calculations
For businesses with unpredictable sales or unreliable suppliers, advanced formulas offer more control. One common version is:
This combines demand variability (σD) and lead time variability (σLT), along with averages for both. If your supplier lead times shift regularly or demand fluctuates wildly, this method keeps your inventory steady without overstocking.
The right formula depends on your inventory flow, supplier consistency and how much risk you’re comfortable with. Fine-tuning your safety stock calculations ensures you’re prepared without tying up too much capital.
Factors to consider when determining safety stock levels
Factor | Considerations | Impact on safety stock |
Lead time variability | Supplier lead times can be inconsistent, especially with international suppliers or complex supply chains. | Higher safety stock levels buffer against delays and supply chain disruptions. |
Demand fluctuations | Seasonal trends or sudden demand spikes can deplete inventory faster. Unpredictable sales patterns require adjustments to safety stock levels. | Accurate forecasting and historical data help determine the right amount of extra stock. |
Service level goals | A higher service level means fulfilling orders without delay more frequently, but it requires more safety stock to handle unexpected demand surges. | More stock improves service reliability, but increases carrying costs. |
Cost of holding inventory | Storing excess inventory incurs costs such as storage, insurance, and tied-up capital in unsold goods. | Balance between stockout prevention and managing storage costs is essential. |
Summary of key considerations
- Lead time variability: Unreliable or lengthy supplier lead times need higher buffers.
- Demand fluctuations: Seasonal or erratic demand requires safety stock adjustments.
- Service level goals: Higher service levels demand more inventory to back them up.
- Cost of holding inventory: Balance the expense of carrying stock with the cost of stockouts.
Each factor plays a role in shaping how much safety stock you need. By analyzing these elements, you can keep your inventory steady without overextending your resources.
Benefits of maintaining safety stock
Ensures smooth operations
Safety stock keeps your business running when the unexpected happens. Sudden dips in inventory levels don’t have to mean halted workflows or missed sales. By acting as a buffer, safety stock prevents downtime that could disrupt your operations or impact your bottom line.
Improves customer satisfaction
Let’s face it: delays and empty shelves frustrate customers, but proper safety stock helps you avoid both. When products are available right when they’re needed, customers can confidently rely on your business. Meeting expectations consistently builds trust, encourages repeat purchases and strengthens your relationship with your audience. What more could you ask for?
Reduces supply chain risks
Supply chains aren’t always predictable. Delayed shipments, supplier hiccups or transport issues can all throw off your inventory plans. Safety stock cushions the blow, ensuring you can fulfill orders without interruptions. It’s a simple way to stay prepared for the inevitable bumps in the road.
Enhances forecasting flexibility
Seasonal trends, sudden surges or minor projection errors can leave you short on stock. Safety stock gives you room to adjust; it provides a buffer that helps you plan with confidence, even when demand shifts unexpectedly.
Tools like Lightspeed Insights can empower businesses with clear, actionable data to optimize their inventory strategies. Detailed reports and eagle-eye forecasting can help retailers track trends and avoid stockout, ensuring businesses are always prepared for shifts in demand.
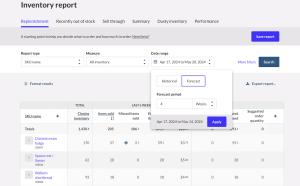
Make data-driven decisions with Lightspeed Insights’ real-time inventory forecasting.
Think of safety stock as more than just extra inventory. It helps maintain steady operations, supports customer satisfaction and ensures you’re prepared for the challenges that go hand-in-hand with growth, so think of it more as a lifeline that keeps your businesses running smoothly.
Challenges of safety stock management
Overstocking risks
Hanging on to too much safety stock takes up space, increases costs and ties up valuable resources. Extra inventory increases carrying costs like storage fees, insurance and even product depreciation. If you’re managing perishable goods or seasonal items, overstocking can quickly turn into unsellable waste, cutting straight into your profit margins.
Balancing cost with risk
Getting the balance right between having enough stock and avoiding excess is tricky. Too little safety stock means stockouts and missed sales, but too much ties up cash flow and impacts efficiency. The key is accurate data and forecasting, along with regular tweaks to keep safety stock aligned with your business needs.
Supplier and demand variability
Unpredictability is where things get complicated. Supplier delays, production issues or demand spikes can throw off even the best inventory plans. When lead times or customer demand fluctuate frequently, safety stock needs constant adjustment—adding complexity to day-to-day operations.
Managing safety stock means walking a fine line. Without a clear strategy, it’s easy to either overstock and waste resources or understock and face avoidable disruptions. A robust inventory management system, like Lightspeed’s POS system, can help businesses track stock levels in real time and adjust safety stock as needed.
Bottom line
Safety stock is at the heart of keeping inventory under control. It protects your business from demand spikes, supplier delays and forecasting errors—helping you avoid costly interruptions. By acting as a cushion, it ensures operations remain smooth and customer expectations are met, no matter the circumstances.
Compared to other strategies like just-in-time inventory or reorder points, safety stock offers more flexibility when uncertainty strikes. Just-in-time minimizes inventory, and reorder points signal when to restock—but neither accounts for sudden demand changes or supply chain hiccups. Safety stock steps in where those strategies fall short, making it ideal for unpredictable demand or when consistent service is non-negotiable.
The key is balance. Combine safety stock with accurate forecasting and inventory tools to avoid overstocking while staying prepared. Talk to an expert to see how it can streamline your inventory and support your growth.
FAQs
What is safety stock EOQ equal to?
Safety stock and EOQ (Economic Order Quantity) are not the same but work together in inventory planning. EOQ calculates the ideal order size to minimize total costs—like holding and ordering expenses. Safety stock, on the other hand, is your backup supply, ensuring you can handle unexpected demand or supplier delays.
What is Z in safety stock?
Z, or the Z-score, is a statistical value tied to your service level goal. It tells you how much extra inventory you need to avoid running out of stock. For instance, a Z-score of 1.65 corresponds to a 95% service level—meaning you’re prepared to meet 95% of demand without interruptions.
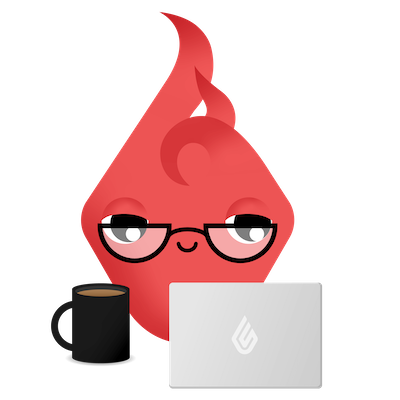
News you care about. Tips you can use.
Everything your business needs to grow, delivered straight to your inbox.