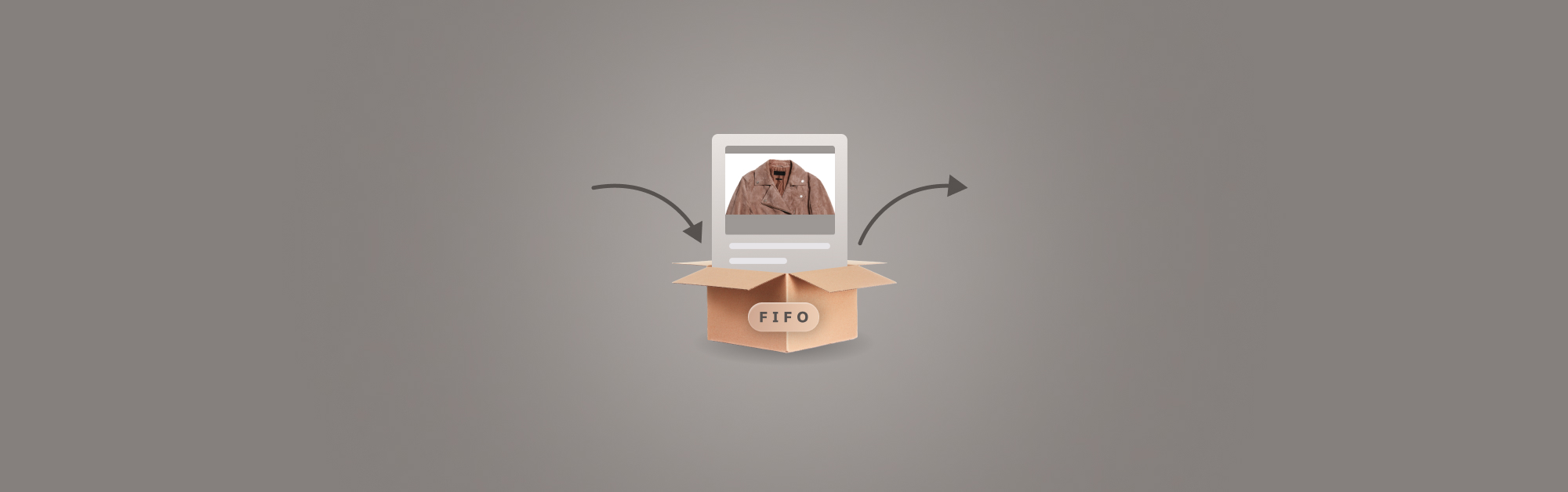
First in first out (FIFO) is one of the most practical inventory methods for businesses managing stock across multiple locations.
As the name implies, FIFO focuses on selling or using the oldest inventory first—keeping operations smooth and ensuring products flow naturally.
This method is fundamental to inventory valuation and calculating cost of goods sold (COGS). By tying outgoing products to their earliest costs, it gives a clearer picture of current inventory value. FIFO also helps businesses avoid issues like spoilage or outdated stock, which is especially useful for perishable or high-turnover items.
Using FIFO also creates consistency across locations and makes financial reporting more straightforward. As inventory needs shift with market trends, FIFO provides an adaptable, structured approach to keep everything on track.
- What is First In, First Out (FIFO)?
- How FIFO works in inventory management?
- Advantages of FIFO
- Disadvantages of FIFO
- When should you use FIFO?
Grow your retail business.
Streamline inventory, suppliers, teams and stores with Lightspeed's all-in-one platform. From intuitive POS and stock management features to powerful reporting, Lightspeed gives you the tools you need to grow.
What is First In, First Out (FIFO)?
First in first out (FIFO) is an inventory method where the oldest stock is sold or used first, leaving newer inventory for later. It’s straightforward and mimics the natural flow of goods—what comes in first goes out first. This method is especially useful for products with expiration dates or those that quickly lose value.
Think about how grocery stores handle inventory. When stocking milk, employees push the older cartons to the front and place newer ones in the back. Shoppers naturally grab the front ones first, which means older inventory sells before it expires. It’s a simple way to reduce waste and keep shelves fresh.
Industries that depend on product freshness or compliance often rely on FIFO. Food and beverage businesses use it to manage perishable goods, while retailers selling seasonal items like clothing or electronics avoid outdated stock by doing the same. Even manufacturing and healthcare sectors benefit—FIFO ensures raw materials or pharmaceuticals are rotated properly and their costs are tracked accurately.
Beyond managing physical goods, FIFO plays a critical role in financial reporting. It ties sales to the oldest inventory costs, creating consistency in valuations. For businesses juggling growing stock levels or multiple locations, FIFO simplifies inventory flow, minimizes waste, and keeps records reliable.
How FIFO works in inventory management?
FIFO assigns the cost of your oldest inventory to the cost of goods sold (COGS) first, while newer stock stays in inventory. It’s straightforward—products are sold or used in the same order they arrive. In a warehouse, this often means organizing stock so the oldest items are picked and shipped first to avoid waste and ensure freshness.
FIFO vs LIFO
How does FIFO compare to LIFO? LIFO (Last In, First Out) works differently. It assigns the cost of your newest inventory to COGS first, leaving older stock untouched. While LIFO can reduce taxable income in inflationary markets by increasing COGS, it doesn’t align with how goods typically move in a business. It also increases the risk of older stock becoming outdated or unsellable.
For businesses dealing with perishable goods or products with expiration dates, FIFO reduces spoilage. Because it prioritizes the oldest items, it ensures inventory quality and keeps shelves moving. On the financial side, FIFO provides a clearer picture of inventory value. Since remaining stock reflects the most recent purchase costs, financial statements are more aligned with current market conditions. This is especially useful during inflation, when older inventory costs are lower and profits are higher.
FIFO keeps operations efficient and records reliable. It’s a system that handles stock the way most businesses already do—first in, first out.
Advantages of FIFO
Reduces obsolescence
FIFO helps prevent inventory from becoming outdated by ensuring the oldest stock is always sold or used first. This approach matters most for products with shorter lifespans, like seasonal items or technology that quickly evolves. By keeping inventory fresh, businesses can avoid markdowns, wasted goods and the costs of holding unsellable stock.
Better for perishable goods
For industries like food, beverages and pharmaceuticals, FIFO is non-negotiable. It prioritizes selling older inventory first, cutting down on spoilage and maintaining product quality. It also helps businesses meet health and safety regulations, which often require strict product rotation to protect customers and avoid compliance issues.
Accurate accounting and costing
FIFO gives a clean, consistent view of inventory costs by tying outgoing stock to its earliest purchase price. Financial reports become more reliable, with accurate cost of goods sold (COGS) and inventory valuations. In times of inflation, FIFO often leads to higher net income—older, lower-cost items are expensed first, leaving newer, higher-cost stock reflected on the balance sheet.
Simplicity in execution
FIFO is straightforward to adopt, which makes it a practical choice for small and medium-sized businesses. It naturally fits how most inventory moves, so it doesn’t require major changes to storage or tracking systems. With inventory management software, FIFO becomes even more seamless, supporting businesses as they grow without complicating operations.
Disadvantages of FIFO
Increased storage costs
FIFO can lead to higher storage costs when older inventory doesn’t sell as planned. Those unsold products take up valuable space, and the longer they sit, the more expensive it gets to store them. For businesses managing large inventories, even a small delay in turnover can quickly drive up operational costs.
Inefficiency in high-volume warehouses
In high-volume warehouses with constant inventory movement, keeping FIFO running smoothly can be a challenge. Older stock needs to stay accessible at all times, which means careful organization and ongoing stock rotation.
Potential for stock mismanagement
Stock mismanagement is another risk—especially if newer products are easier to access than older ones. When inventory isn’t rotated properly, older items can be overlooked, leading to waste, spoilage or outdated products. Over time, this misstep can erode profitability and create additional storage headaches.
Inflated profit reporting in times of inflation
During inflation, FIFO’s reliance on older, lower-cost inventory can make profits appear higher than they actually are. While that might look good on paper, it often means paying higher taxes—something businesses with tight margins can’t afford to overlook. The short-term boost in profits may come with long-term financial strain.
These challenges don’t mean FIFO isn’t effective, but they highlight why it’s not a one-size-fits-all solution. Careful planning and the right tools are essential to ensure FIFO works for your specific operational needs.
When should you use FIFO?
FIFO is a smart choice when inventory needs to move fast to stay fresh or meet strict regulations. Food and beverage businesses depend on it to avoid spoilage and keep shelves stocked with fresh products. It’s the same for industries like pharmaceuticals or cosmetics, where expiration dates are critical for safety and compliance.
It’s also a great fit for seasonal or high-turnover products. FIFO makes sure older inventory sells first, cutting down on markdowns or unsellable stock. Apparel retailers, for example, can use it to rotate through collections and avoid holding onto outdated styles. During inflation, FIFO can help on the financial side too. It ties sold goods to older, lower costs—boosting profitability on paper.
But FIFO isn’t always the best option. For non-perishable goods that don’t lose value over time, LIFO (last in, first out) might make more sense. LIFO flips the script, selling newer inventory first and lowering taxable income by raising the cost of goods sold (COGS). Weighted average costing can also work well if your products are indistinguishable or often mixed, like raw materials or bulk items.
The right method depends on what matters most to your business. Think about how quickly your items need to sell, how compliance impacts your operations, and how taxes or profit margins play into your financial goals. Aligning your inventory method with your priorities keeps your business running smoothly while supporting long-term growth.
Bottom Line
The FIFO inventory method is simple and mirrors the natural flow of goods. By selling older stock first, it reduces waste, avoids spoilage and ensures compliance with products that have expiration dates. It also brings financial clarity—older costs tie directly to cost of goods sold (COGS), keeping inventory valuations consistent and reliable.
FIFO works especially well for businesses handling perishable items, seasonal products or high-turnover inventory. It keeps operations efficient and protects profitability, particularly during inflation when lower-cost inventory is expensed first. But staying organized is key—poor tracking or storage can lead to mismanaged stock or higher costs.
The right inventory method depends on your business needs, product types and financial priorities. Watch a demo to learn how the right tools can streamline your process and keep your business growing.
FAQs
What’s the difference between FIFO and LIFO?
FIFO, or first in first out, is all about using or selling the oldest inventory first—it follows the natural flow of goods. LIFO, or last in first out, flips the process by prioritizing the newest inventory instead, leaving older stock untouched for longer. To see how they compare in terms of financial and operational impact, check out our guide on FIFO vs. LIFO: Comparing Inventory Valuation Methods.
What are the challenges of implementing FIFO in large warehouses?
Large warehouses come with unique challenges when using FIFO. Keeping older stock accessible requires precise organization, which often means adjusting layouts or investing in storage systems designed for this method. Without proper planning, inefficiencies in picking processes can slow operations and lead to errors like stock getting overlooked or wasted.
How can FIFO help reduce waste in inventory management?
FIFO reduces waste by ensuring older stock moves out first, lowering the risk of spoilage or obsolescence. It’s especially effective for managing perishable items or products with expiration dates, like food or pharmaceuticals. By keeping inventory in the right order, businesses can minimize losses and save on costs tied to unsellable goods.
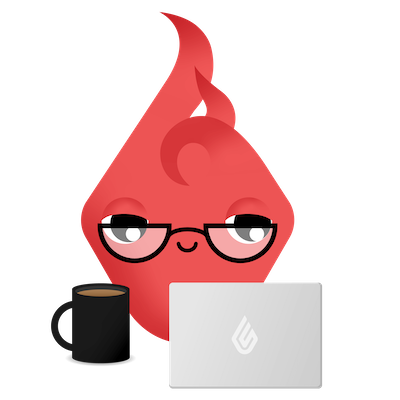
News you care about. Tips you can use.
Everything your business needs to grow, delivered straight to your inbox.