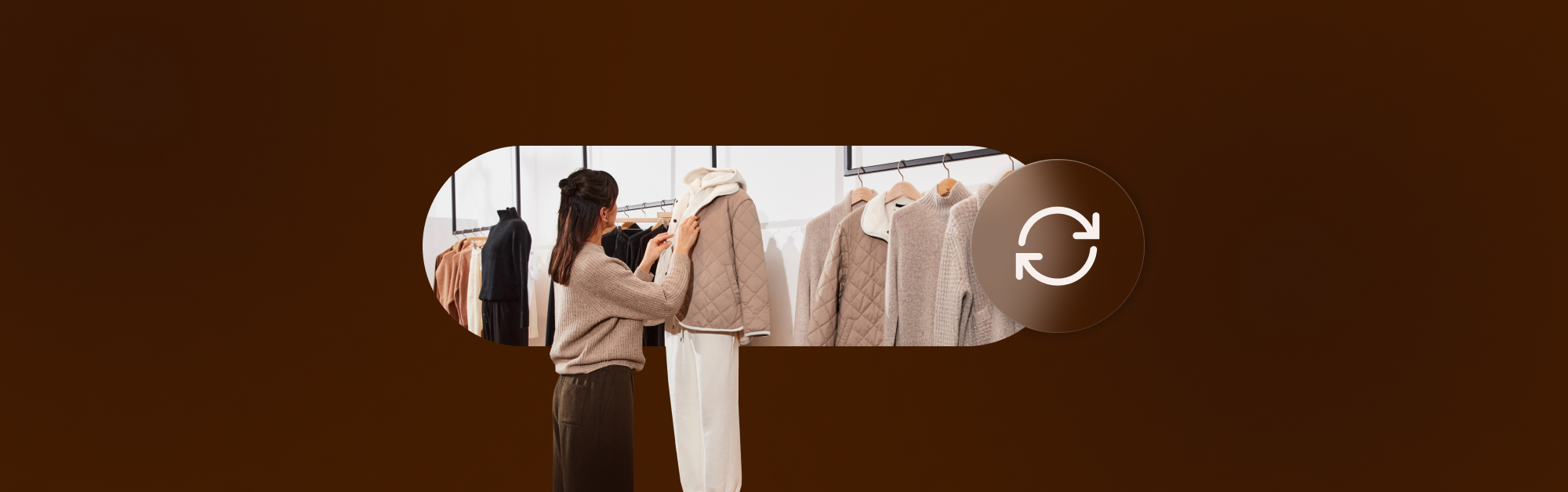
Cycle stock, the portion of your stock set aside specifically to meet regular demand during a defined period, is a key part of managing inventory for retail and hospitality businesses. Without it, businesses can face stockouts, operational inefficiencies and unhappy customers—a scenario no retailer wants.
For businesses with multiple locations or sales channels, keeping inventory in check can feel overwhelming. Cycle stock simplifies the process by setting a clear baseline of inventory needed to handle everyday sales. It also helps balance how often you reorder and how much space you need for storage.
Getting cycle stock levels right is more than just a numbers game. It keeps cash flow steady, ensures resources are used wisely and lets you meet customer demand without tying up money in unnecessary stock.
In this blog, we’ll go over:
- What is cycle stock?
- Why is cycle stock important to inventory management?
- Cycle stock vs. safety stock
- How to calculate and manage cycle stock
- Advantages of effective cycle stock management
- Potential challenges of managing cycle stock
Grow your retail business.
Streamline inventory, suppliers, teams and stores with Lightspeed's all-in-one platform. From intuitive POS and stock management features to powerful reporting, Lightspeed gives you the tools you need to grow.
What is cycle stock?
Cycle stock—sometimes called working inventory—is the portion of inventory you rely on to meet expected customer demand over a set period. It’s what businesses regularly sell and replenish, making it the backbone of day-to-day inventory management. Unlike other types of stock, it’s not meant to handle surprises. Instead, it’s a planned amount designed to keep up with predictable sales.
In practice, cycle stock plays a critical role in ensuring smooth business operations. It directly affects how often you reorder, how much space you need for storage, and how well your cash flow is managed. When cycle stock levels are balanced, businesses can minimize unnecessary ordering costs, maintain steady inventory turnover, and avoid the risk of stockouts that frustrate customers.
What cycle stock isn’t
It’s important to distinguish cycle stock from safety stock and anticipation inventory. Safety stock acts as a buffer for unexpected spikes in demand or supply chain delays. Anticipation inventory, on the other hand, is extra stock businesses order ahead of seasonal peaks or special events. Cycle stock isn’t about preparing for the unexpected—it’s about meeting the routine demand that keeps operations steady.
Why is cycle stock important to inventory management?
Maintaining operational efficiency
Cycle stock keeps daily operations moving. It ensures businesses have enough inventory to meet regular demand without stalling production or sales. Without it, supply chain bottlenecks are inevitable—and that means delays, lost revenue and frustrated customers.
Cost-effective inventory management
Managing cycle stock effectively avoids the hidden costs of overstocking. Excess inventory takes up space, drives up storage costs and risks becoming obsolete. By keeping just the right amount of stock on hand, businesses lower expenses while staying ready for customers.
Reducing order frequency
Cycle stock lets businesses place fewer, larger orders instead of constant small ones. Bulk ordering saves time, reduces shipping costs and eases the administrative workload. It also creates predictable ordering patterns, which strengthens supplier relationships and smooths out procurement.
Optimizing cash flow
Too much inventory ties up cash that could be used for growth—like marketing or hiring. Cycle stock strikes the right balance, keeping enough inventory to meet demand without draining resources. This balance protects cash flow, giving businesses more flexibility to invest where it matters most.
Cycle stock vs. safety stock
Cycle stock and safety stock play different roles in inventory management. Cycle stock is the inventory you rely on to meet steady, predictable demand over a set period. It’s part of your regular operations—used, sold, and replenished on a routine schedule based on forecasts and order patterns.
Safety stock is there for the unexpected. It’s extra inventory held as a backup to handle surprises like sudden demand spikes or supplier delays. Unlike cycle stock, safety stock isn’t part of your normal turnover—it’s a safeguard to keep things running smoothly when plans go off track.
Key differences between cycle stock and safety stock
- Purpose: cycle stock supports routine demand, while safety stock cushions against unpredictability in supply or demand.
- Usage frequency: cycle stock moves regularly as part of day-to-day operations. Safety stock is only used when disruptions occur.
- Calculation factors: cycle stock is based on forecasted demand and reorder schedules. Safety stock accounts for lead times, demand variability and service level goals.
When to use each?
Think of cycle stock as the foundation of your inventory—it’s what keeps shelves stocked and operations moving without interruption. Safety stock, on the other hand, is your safety net. It steps in when something unexpected happens, like a delayed shipment or a sudden sales surge.
Balancing both is key. Too much cycle stock ties up cash and space, while too little safety stock leaves you vulnerable to stockouts. Together, they ensure you’re prepared for both the routine and the unpredictable.
How to calculate and manage cycle stock
To calculate cycle stock, start with a simple formula: Cycle Stock = Average Inventory – Safety Stock.
Average inventory is the total stock you typically hold during a replenishment cycle. Safety stock, on the other hand, is your buffer for unexpected demand or supply chain delays. The difference between the two gives you the inventory reserved for meeting predictable, everyday demand.
Several factors determine how much cycle stock you’ll need. Demand variability—how much your sales fluctuate—plays a big role. Steady demand means smaller cycle stock, but if sales are unpredictable, you’ll need more to avoid stockouts. Then there’s lead time, which is the time it takes for suppliers to deliver new inventory. Longer lead times usually mean holding more cycle stock to cover the gap between orders. Finally, order size matters. Larger orders increase stock on hand initially but reduce how often you need to reorder.
The Economic Order Quantity (EOQ) formula helps you find the sweet spot for cycle stock. EOQ strikes a balance between ordering costs (like time and admin work) and holding costs (like storage and insurance). By using EOQ, you can figure out how much to order at once to minimize costs while keeping enough inventory to meet demand. For instance, if EOQ recommends ordering 500 units, your cycle stock naturally adjusts to maintain this flow, ensuring you never have too much—or too little—on hand.
Use technology to save time managing cycle stock
Calculating cycle stock—and keeping an eye on your stock levels—is time consuming when done manually. Some retailers opt to go without managing cycle stock entirely, putting themselves in a reactionary position instead of a proactive one.
That’s why it’s important to use a POS that can track reorder levels and forecast orders for you.
Lightspeed’s inventory management software suggested order quantity is calculated based on your sales data to help keep your cycle stock at optimal levels.
4 advantages of effective cycle stock management
1. Improves inventory turnover
When cycle stock aligns with regular demand, inventory moves faster—no more dusty shelves filled with products that don’t sell. Higher turnover rates free up storage space and reduce the risk of products becoming outdated or unsellable. It’s a simple rule: inventory that moves quickly is inventory that works for your business.
2. Reduces holding costs
Excess inventory costs money. Cycle stock management keeps storage needs in check by maintaining just enough inventory to meet demand. Lower stock levels mean lower expenses for warehousing—like rent, utilities and insurance—and fewer resources wasted on items that sit around instead of selling.
3. Simplifies replenishment
Predictable ordering patterns are one of the biggest perks of managing cycle stock well. Regular cycles make it easier to plan purchases, saving time on calculations and reducing the stress of last-minute orders. Suppliers benefit too—consistent orders build stronger partnerships and reduce the risk of delays.
4. Enhances demand forecasting
Getting cycle stock right depends on accurate demand forecasting. By focusing on routine demand, businesses can fine-tune their forecasts and improve inventory accuracy. Over time, this allows for better planning, fewer stockouts and a clearer view of trends that help guide smarter decisions.
Potential challenges of managing cycle stock
Demand variability
Customer demand isn’t always predictable. Sudden spikes—caused by seasonal trends or unexpected market shifts—can push cycle stock levels below what’s needed. When forecasts miss the mark, stockouts happen and businesses are left scrambling to keep up. Regular reviews and adjustments are the only way to avoid losing sales or disappointing customers during high-demand periods.
Supply chain disruptions
Even the best-planned inventory can’t handle every supply chain hiccup. Delayed shipments, supplier shortages, or transportation bottlenecks cause replenishment delays that throw off the balance. If cycle stock isn’t adjusted for longer lead times, shelves can go empty fast—and customers notice. Planning ahead for disruptions is critical to keeping operations steady.
Overstocking
Too much inventory is just as damaging as too little. Overstocking ties up cash in products that don’t sell, driving up storage costs and increasing the risk of outdated or expired items. This is especially problematic for goods with short lifecycles. Finding the right balance between having enough stock and avoiding excess is key to keeping costs down and profits up.
Bottom line
Cycle stock is what keeps inventory flowing smoothly. It’s how businesses meet regular demand without overloading storage or tying up cash. The right balance keeps operations efficient, reduces costs, and frees up resources for other priorities.
Managing cycle stock isn’t something you set and forget. It means regularly assessing demand, lead times, and order sizes to keep everything on track. When done well, it prevents stockouts, cuts waste, and keeps profitability in check. It’s not just about having enough inventory—it’s about creating a system that works efficiently and predictably.
Talk to an expert to see how you can streamline inventory management and grow your business.
FAQs
Is EOQ the same as cycle stock?
EOQ (Economic Order Quantity) and cycle stock aren’t the same, but they’re connected. EOQ is a calculation that pinpoints the ideal order quantity to keep ordering and holding costs as low as possible. Cycle stock, however, is the inventory you use and replenish consistently to meet everyday demand. In short, EOQ decides how much to order, while cycle stock is what keeps your operations running smoothly between those orders.
What is cycle stock also called?
Cycle stock is often called working inventory. The name reflects its purpose—it’s the inventory you rely on daily to handle predictable demand. Unlike safety stock, which serves as a backup for the unexpected, working inventory keeps the regular flow of orders and replenishments on track.
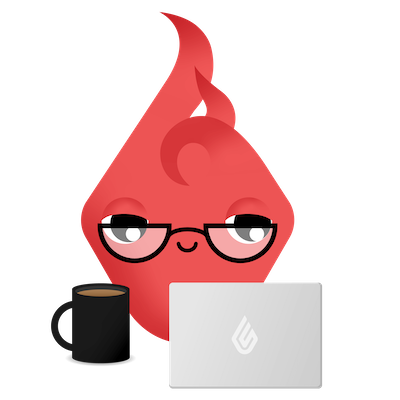
News you care about. Tips you can use.
Everything your business needs to grow, delivered straight to your inbox.