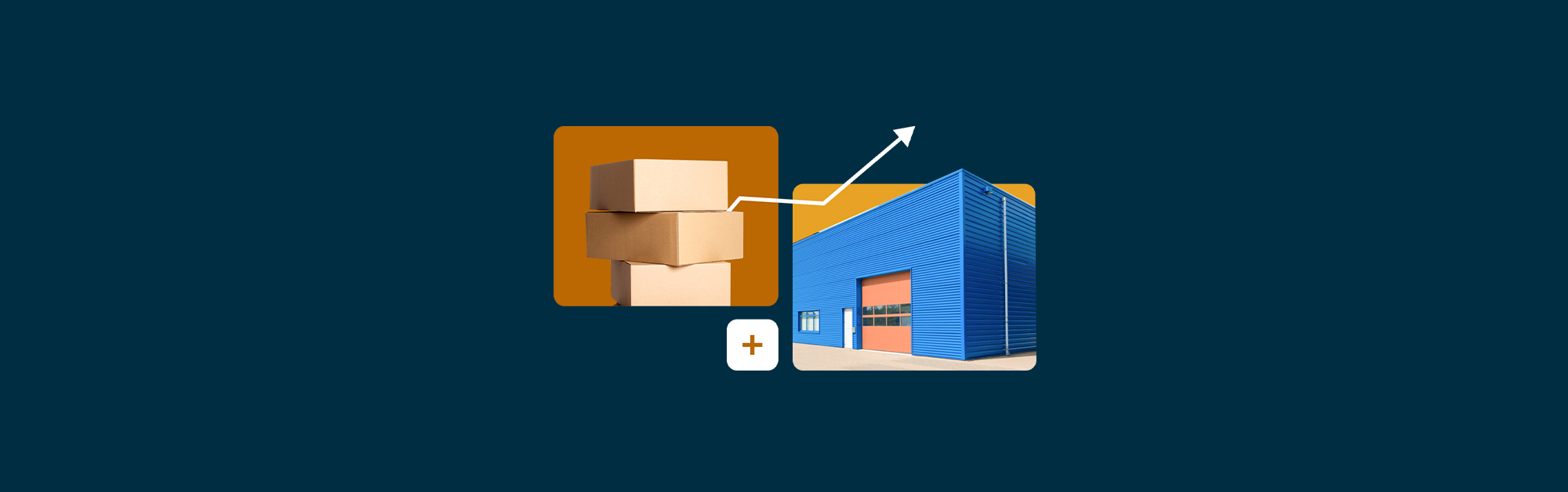
Effective warehouse inventory management is table stakes for today’s retailer. With the right system in place, you gain real-time visibility and control over your stock, helping you stay ahead of demand and competition. Without it, you risk costly mistakes, operational delays and losing customers due to stockouts and slow order fulfillment.
Traditional inventory tracking methods can lead to errors that can disrupt your entire operation. Overstocking ties up capital and space, while understocking results in missed sales and unhappy customers. These inefficiencies not only impact your bottom line but also your ability to meet changing consumer and market demands.
That’s where a powerful inventory management system comes in. Keep reading to learn more about warehouse management systems (WMS) and how they can revolutionize your operations.
In this blog, we’ll cover:
- Why is warehouse inventory management important?
- The role of inventory management software in warehouses
- Top 8 warehouse inventory management system benefits
- Upgrading your warehouse management system
Why is warehouse inventory management important?
Inventory management is crucial in warehouses because it ensures that the right products are available in the right quantities at the right time, helping retailers to avoid overstocking and understocking. With real-time inventory data, warehouses can fulfill orders promptly, minimize dead stock and maintain optimal stock levels, ultimately increasing customer satisfaction and profitability.
Good inventory management also reduces the risk of errors and discrepancies, boosts productivity and enables better decision-making through data insights. It supports seamless coordination across different sales channels, ensuring that inventory is accurately reflected, whether it’s for in-store purchases or online orders. As any retailer knows, this is essential for maintaining a smooth supply chain and meeting your customers’ expectations.
To stay ahead in today’s fast-paced market, consider implementing our Warehouse Efficiency Tips. This resource offers valuable techniques for optimizing your storage layout and enhancing order fulfillment, ensuring your operations run smoothly.
What is the role of inventory management software in warehouses?
Inventory management software in warehouses helps automate the tracking and management of inventory. Instead of endless physical counts and spreadsheets, employees can quickly and accurately record goods as they arrive, are stored and shipped out using tools like barcode scanners and RFID tags. For instance, when a shipment arrives, staff scan barcodes on each item, instantly updating the system with new stock levels. This eliminates manual data entry errors and provides an up-to-date view of inventory.
The software also optimizes warehouse operations by organizing and managing stock locations. It can suggest the best storage spots for items based on size, demand or accessibility. For example, fast-moving products can be stored closer to the packing area for quicker retrieval. This helps streamline the picking and packing process, reducing the time it takes to fulfill orders and enhancing overall productivity.
It also plays a key role in labor optimization in warehouses. By automating routine tasks like inventory counts and stock location updates, the software frees up staff to focus on higher-value activities—a game-changer for both your productivity and labor costs.
Inventory management software also provides retailers with valuable insights through reporting and analytics. With the right software, you can track sales trends, monitor stock levels and forecast demand more accurately. So, if data shows a spike in demand for a particular product, you can reorder before stock runs out, ensuring you have enough inventory to meet demand (but not so much that you can never move it).
Learn how to choose a Warehouse Management System that aligns with your business needs by exploring our detailed guide.
8 key benefits of inventory management software in warehouses
The benefits of inventory management systems in warehouses are numerous—but here are our top eight:
1. Improved accuracy and fewer errors
Warehouse inventory management software significantly minimizes human error by automating key processes like inventory tracking and management. Features such as real-time tracking, barcode scanning and automated stock updates helps to ensure that your stock levels are accurate and up-to-date. Instead of manually entering data every time a product is received or shipped, staff can simply scan barcodes, reducing unnecessary labor hours and costly mistakes, like shipping the wrong product or overstocking slow-moving items.
2. Better productivity and efficiency
Automation lets your staff focus on more high-value tasks than repetitive manual inventory counts. This not only speeds up order fulfillment but also improves overall warehouse management. With a warehouse inventory management system in place, staff can quickly locate and pick items, reducing the time it takes to process orders and ensuring timely order delivery for customers.
3. Better decision-making with data insights
With real-time tracking and automated stock management, a warehouse management system (WMS) maintains high levels of inventory accuracy—crucial for avoiding overstocking and stockouts. Integrating your WMS with sophisticated inventory management software can extend your capabilities, giving you full visibility into your inventory across multiple locations and channels. Using inventory management software with your WMS will also give you more detailed inventory data, enabling more in-depth analysis, more accurate demand forecasting and smarter purchasing decisions.
4. Cost savings
Optimized inventory levels, reduced waste and better resource allocation can lead to significant cost savings. By automating inventory tracking and reducing the need for manual counts, businesses can lower labor costs, avoid tying up too much capital in inventory and reduce the risk of products becoming obsolete, out of style or expiring while stagnating on shelves.
5. Better flexibility and more agile operations
Sophisticated inventory management software is designed to evolve with your business. One of the key benefits of this software is that it can be updated or configured to handle new challenges, so you can adapt quickly to changing market conditions, or add new functionalities as your business needs change.
6. Scalability
Warehouse inventory management software provides scalability, allowing retailers to easily expand their operations without overhauling their systems. Whether you’re opening new locations, adding new products or increasing order volumes, the right inventory management software can scale up to meet these demands without compromising on efficiency or accuracy.
7. Compliance and reporting
For industries with strict regulations, like pharmaceuticals or food and beverage, end-to-end traceability is crucial. Warehouse management systems provide comprehensive tracking from the moment a product enters the warehouse to when it is shipped out. This traceability helps ensure compliance with regulatory requirements and makes reporting and audits more straightforward and reliable.
8. Streamlined operations and integration
Seamless integration with other systems allows for a unified view of inventory across different sales channels. This integration ensures that all sales channels accurately reflect inventory levels, reducing the risk of overselling and enhancing the customer experience. For retailers, this means smoother operations and a more cohesive approach to managing your business.
Upgrade your warehouse management system with Lightspeed
While a WMS tracks inventory as it flows in and out of the warehouse, retailers with multiple locations or vast product catalogs often need more granular data and greater visibility across their operations. That’s where sophisticated inventory management software like Lightspeed comes in.
Lightspeed offers a premium retail POS and inventory management solution tailored to modern retail demands. It can work independently, or alongside your WMS, to help you accurately track and manage inventory across all your locations and sales channels in real time.
“With Lightspeed, [all our offsite locations communicate together and are tied into the cloud], so we can track inventory across areas and transfer between locations… Every week, we do inventory transfers and it uses the reorder quantities baked into Lightspeed and it just pulls up what we need to bring down. We do an office order and our staff picks it up from the warehouse and brings it over and it makes it really easy and intuitive and quick.” — Andy Linn, Founder, City Bird
Online, in-store, in warehouses or distribution centers, Lightspeed makes it easy to see exactly what you have, what you need, what’s selling and what’s gathering dust—so you can better forecast demand, boost efficiency and adjust your buying, pricing or marketing strategies as needed. As transactions are processed at the point of sale, stock levels automatically update in real time, reducing the risk of overselling or stockouts.
“We’re able to pull a report of the top 100 products across our locations so that a new owner has a readily available inventory to choose from. With Lightspeed, this is quite easy to do and very helpful when we’re trying to open new locations. We are expanding and we’re going to continue to expand. It’s just that easy if you want to become a multi-location business.” — Angela Logan, Systems Coordinator, Simply for Life
Lightspeed also seamlessly integrates with other business tools and platforms—your ecomm store, WMS, ERP, labor management software, accounting software, you name it—providing a unified view of sales, inventory and customer data. It’s one platform to rule them all. (And by that, we mean manage all aspects of your business.)
“We don’t double sell with ecommerce, as when an action happens in one system it’s automatically recorded in the other. And we save time because we only enter the product information once, and it’s available across both systems. Everyone is happy.” — Michael Nagdimunov, Owner, Grain & Vine
With its suite of smart inventory management features, including the only closed-loop B2B trade network on the market, Lightspeed makes it (way) faster and easier for retailers to handle large inventories and complex product catalogs. Learn more about Lightspeed Retail.
Bottom line
Warehouse management software offers retailers significant benefits, including more accuracy, enhanced productivity and better decision-making through real-time data insights. It helps reduce errors, optimize labor and streamline operations, ultimately helping you lower your costs and improve customer satisfaction.
By integrating a powerful inventory management solution like Lightspeed, retailers can take their warehouse inventory management to the next level with features like multi-location inventory tracking, automated stock updates and seamless integration with other locations and sales channels. Lightspeed not only simplifies inventory management but also provides the flexibility and scalability needed to support your retail business as it grows.
Want to see Lightspeed’s all-in-one retail platform in action? Book a demo with us today.
FAQs
Why is a warehouse management system (WMS) important?
A WMS is crucial for optimizing warehouse operations, improving inventory accuracy and enhancing productivity. Advantages of warehouse management systems include streamlining processes such as receiving, storing, picking and shipping, leading to better overall efficiency and cost savings.
What are the basic warehouse operations?
Essential warehouse operations encompass the day-to-day activities required to efficiently manage the flow and storage of goods within a warehouse. These activities typically include:
- Receiving: Inspecting and verifying incoming shipments to ensure they match purchase orders and are not damaged.
- Putaway: Moving received goods to designated storage areas, helping maintain organization and accessibility.
- Storage: Organizing goods in a way that maximizes space and facilitates easy retrieval while preventing damage or loss.
- Picking: Selecting items from storage based on customer orders, a crucial step for ensuring order accuracy.
- Packing: Preparing selected items for shipment with appropriate packaging to safeguard them during transit.
- Shipping: Coordinating the dispatch of packed orders, including transportation logistics and necessary documentation for delivery.
- Inventory control: Continuously monitoring stock levels to balance supply with customer demand, avoiding overstock and stockouts.
What’s the difference between warehouse management software and inventory management software?
Warehouse management software and inventory management software are related but serve distinct purposes within supply chain and warehouse operations.
Warehouse management software is designed to manage the entire warehouse operation, from receiving and storing goods to picking, packing and shipping them. It includes functionalities like inventory tracking, warehouse layout management, labor management, task scheduling, location tracking, order picking optimization and shipping logistics. It provides a comprehensive view of the warehouse, focusing on optimizing the movement and storage of goods within the facility.
Inventory management software, on the other hand, focuses on tracking and managing your product catalog and inventory levels, orders, sales and deliveries across various locations, including warehouses, retail stores and distribution centers. It includes functionalities like real-time inventory tracking, automated reordering, barcode scanning, purchase orders, stock transfers and advanced insights and reporting. Inventory management software enables retailers to track inventory across multiple locations, focusing on inventory quantities and movement rather than warehouse-specific operations.
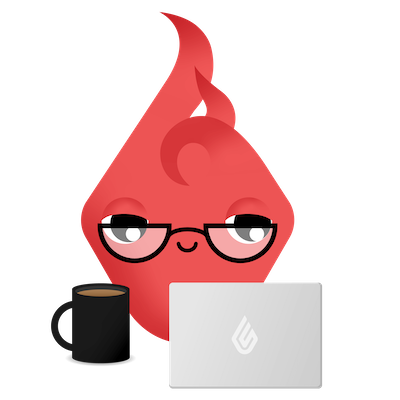
News you care about. Tips you can use.
Everything your business needs to grow, delivered straight to your inbox.