7+ Warehouse Efficiency Tips to Keep Your Operations and Warehouse Management System Running Smoothly
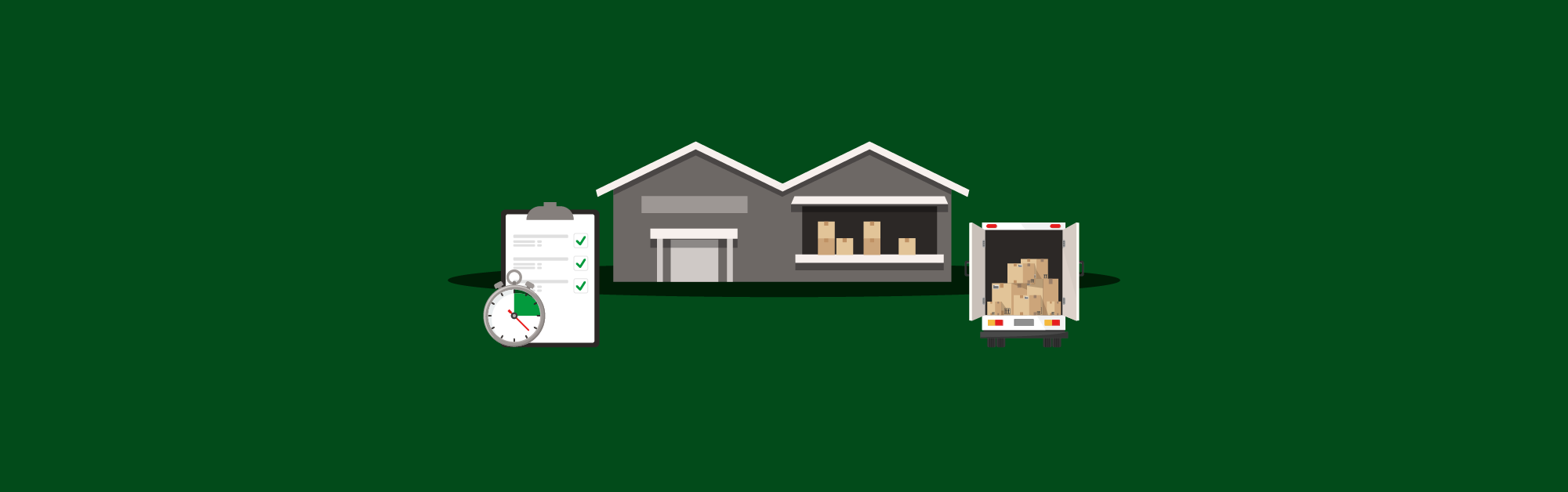
Efficient warehouse stock management, guided by the right warehouse efficiency tips, can make or break your business. Without it, you risk falling behind; with it, you gain real-time control and the power to outpace your competition.
Poor stock management can ripple across your business operations, leading to significant financial losses, operational inefficiencies and perhaps most damagingly, customer dissatisfaction. When items are mismanaged, out-of-stock or delayed, it not only impacts sales but also erodes trust in your brand. One McKinsey study found that only 13% of shoppers are willing to wait for you to restock—they’re far more likely to switch brands instead.
The answer? A robust warehouse stock management system that can transform these challenges into opportunities for growth and reliability.
In this blog, we’ll cover:
- What warehouse management is
- Why warehouse management is important
- 7 best practices for efficient warehouse management
- How to choose the right warehouse management system
The Value of a Unified Payments and POS Solution
An in-depth look at how a streamlined platform for payment processing can transform the way you operate your business, especially compared to legacy systems and patchwork solutions.
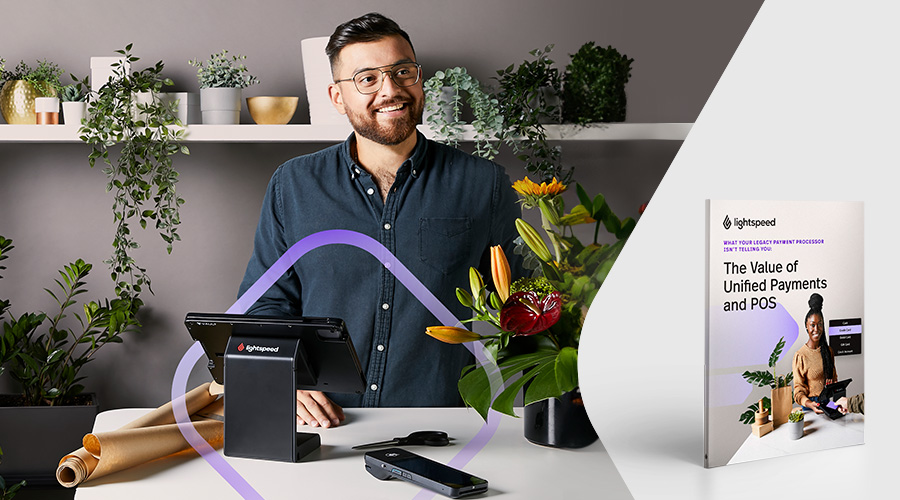
What is warehouse management?
Warehouse management is a system for handling all aspects of operations within a warehouse or distribution center. Its purpose is to streamline processes and ensure efficient workflow.
At its core, warehouse management involves managing and optimizing a range of functions, from inventory control to order fulfillment, each playing a crucial role in the overall business strategy.
When it comes to optimizing warehouse operations, knowing how to choose a warehouse management system can significantly impact your efficiency and productivity. A warehouse management system will have tools and processes for:
- Receiving and putaway: the first steps in the warehouse cycle involving the acceptance of incoming goods and their correct placement in the warehouse. Efficient processes here are essential to prevent bottlenecks later on
- Inventory control: maintaining accurate records of all items entering and leaving the warehouse, ensuring that stock levels are sufficient to meet demand without overstocking, which can tie up capital unnecessarily
- Storage optimization: the strategic placement of goods within a warehouse to maximize space utilization and minimize retrieval time
- Order fulfillment: ensuring that customers receive their products promptly and accurately, which is critical for maintaining customer satisfaction and loyalty
- Technology integration: systems like Warehouse Management Systems (WMS), point of sale (POS) software, barcode scanners and RFID technology to enhance accuracy and speed up operations
- Labor management: scheduling and deployment of warehouse staff to maintain productivity and meet operational demands
- Safety and compliance: ensuring that operations adhere to legal standards and work practices to keep staff safe and avoid penalties
Consider a furniture retail business: efficient warehouse management ensures that a popular sofa model is always in stock, stored safely in a way that prevents damage and can be easily picked and shipped when an order is placed online. This impacts not just logistics but also sales, customer service and ultimately brand reputation.
Why is warehouse inventory management important?
Warehouse inventory management helps businesses optimize operations, reduce costs and enhance customer satisfaction—and more.
Reduced costs
Did you know US retailers are sitting on $740 billion in unsold goods? That’s a lot of stuck inventory driving up costs—costs to store, manage and track products that aren’t selling.
Proper inventory management helps reduce carrying costs, including storage fees, insurance and potential spoilage, by ensuring that stock levels are just right—not too high and not too low. This balance minimizes waste and reduces the financial burden on the company.
Increased productivity
Effective inventory management ensures that stock levels are accurately recorded, which prevents overordering and understocking.
This accuracy helps streamline the picking and packing processes, thereby boosting productivity. Workers spend less time searching for items or dealing with stock discrepancies.
Improved accuracy
Warehouse inventory management systems often utilize technologies like barcode scanning and RFID tracking to ensure every item is accurately logged as it moves in and out of the warehouse. This precision eliminates errors in stock counts, reducing the instances of mispicks and misships that can occur due to incorrect inventory data.
Faster shipping
Efficient warehouse inventory management streamlines the order fulfillment process by organizing stock in a way that optimizes picking and packing paths.
For example, with Lightspeed, you can record and view where your products are stored at the Aisle, Bay, Shelf and Bin level per outlet right in your retail point of sale. That means less hunting and searching for warehouse staff, speeding up the shipping process.
Real-time inventory updates also help in promptly processing orders and ensuring that items are available and ready to ship, thus minimizing delays and increasing overall shipping efficiency.
Increased customer satisfaction
By managing warehouse inventory effectively, businesses can ensure that products are available when customers need them, thus avoiding backorders and potential sales losses.
7 most competent practices for efficient inventory management
- Prioritize your inventory
- Use identification markers
- Perform regular audits
- Handle stock effectively
- Record your sales
- Streamline your inventory management plan with defined roles
- Use inventory management software
1. Prioritize your inventory
Classify inventory using methods like ABC analysis, which segments items based on their importance and sales volume.
ABC inventory analysis is a technique that divides inventory into three categories (A, B, and C) to determine which items require the most attention and resources.
- Category A includes items that are the most valuable, typically making up a small percentage of inventory but accounting for the majority of the revenue. These require frequent review and tight inventory control
- Category B items are of moderate value, usually constituting a larger percentage of inventory than A items but less critical to revenue. They benefit from regular monitoring but less intensive management
- Category C items are the least valuable, often making up the bulk of inventory numbers but contributing the least to revenue; they require minimal oversight
This categorization helps in focusing efforts and resources on the most financially impactful items, thereby optimizing inventory levels and reducing carrying costs associated with less crucial items.
2. Use identification markings
Implement a labeling system with barcodes or RFID tags to track each item efficiently. This aids in quickly locating goods within the warehouse and speeds up the picking process.
For example, a furniture warehouse might use distinct markings to differentiate between similar-looking items like chairs and tables of different models or colors.
To get the most out of your identification markings:
- Standardize labeling practices: develop a uniform labeling system that includes clear, consistent guidelines on where and how labels should be applied to different types of products
- Incorporate descriptive information: labels should include not just a unique identifier but also essential information such as product type, size, color and handling instructions
- Utilize color coding: add color codes to labels to further enhance the speed and accuracy of the picking process. For example, different colors could represent different product categories or priority levels
- Leverage technology: employ advanced scanning systems and mobile devices, like Lightspeed Scanner, to read barcodes and tags. These technologies speed up the verification and tracking of items through real-time updates to the inventory management system
The Lightspeed Scanner app interface
3. Perform regular audits
Regularly scheduled audits, such as cycle counts, help maintain inventory accuracy by verifying your physical stock against the recorded inventory. This practice catches discrepancies and issues early, reducing the risk of stockouts or overstock situations.
Conducting audits quarterly or even monthly, depending on the size of the operation, can significantly enhance inventory control. To set your audits up for success:
- Set clear objectives: before scheduling an audit, define what you aim to achieve, whether it’s verifying accuracy, assessing compliance with storage procedures, or identifying obsolete inventory
- Use a rotating schedule: implement a rotating schedule for cycle counts so that all inventory is audited over a set period. This approach prevents the disruption of daily operations and spreads the workload evenly across the year
- Train your team: ensure that staff conducting the audits are well-trained in auditing procedures and understand how to use any relevant technology or equipment
- Leverage technology… again: utilize inventory management software and scanning technology (like Scanner) to streamline the audit process
- Review and act on findings: after each audit, review the findings and take appropriate actions to address any identified issues. This could involve adjusting inventory levels, updating records or revising storage practices
4. Handle stock effectively
Develop protocols for handling stock that minimize damage and loss, such as proper stacking techniques and the use of suitable handling equipment.
Make sure to tailor your protocols to the type of stock you’re carrying. Some examples include:
- Electronics warehouse: use anti-static flooring and tools to prevent damage.
- Apparel and textiles warehouse: utilize garment racks and covered bins to protect items from dust and dirt. Ensure that handling staff use gloves to prevent oils or dirt from contaminating the fabrics
- Furniture warehouse: equip with dollies, furniture pads and straps to protect furniture during movement. Stack lighter items on heavier, more stable items and avoid stacking items too high to prevent tipping
- Chemical warehouse: implement spill containment measures and use corrosion-resistant shelving. Workers should wear appropriate safety gear, including gloves and goggles, and materials should be stored according to compatibility
- Heavy machinery warehouse: utilize cranes, forklifts and pallet jacks that are rated for heavy loads. Ensure that aisles are wide enough to accommodate large equipment movement and that floor load limits are strictly adhered to
5. Record your sales
Keeping accurate records of sales helps track inventory levels and predict future demand. This data is crucial for planning purchases and can help avoid excess inventory that ties up capital.
Utilizing point of sale systems that update inventory in real time as sales occur provides a clear picture of stock levels at any given moment.
6. Streamline your inventory management plan with defined roles
Develop a clear, structured plan that outlines processes for purchasing, storing and selling inventory. This plan should include defined roles and responsibilities for your team, like:
- Inventory manager: oversees all aspects of inventory control; coordinates purchasing, monitoring and replenishment activities; ensures accuracy in inventory counts and records
- Purchasing officer: responsible for procuring stock based on the demand forecasts and inventory levels; negotiates with suppliers to secure the best prices and terms
- Warehouse supervisor: manages the day-to-day operations within the warehouse, including staffing, scheduling and ensuring adherence to safety protocols; oversees the receiving, storing, and shipping processes
- Stock handlers: perform tasks related to the physical handling of goods including receiving, storing, picking, and packing; ensure proper handling techniques to minimize damage
- Quality control inspector: checks incoming and outgoing products for quality and compliance with specifications; manages returns of defective items to suppliers
- Data analyst: tracks inventory data and analyzes patterns in stock movement and usage; provides reports that help in making informed decisions about stock management
7. Use inventory management software
Adopting sophisticated inventory management software can automate many aspects of inventory control, from ordering and tracking stock to forecasting demand.
This software can integrate with other systems like CRM and ERP, providing a comprehensive view of business operations and improving decision-making.
For example, software that syncs inventory data across online and physical stores can ensure consistent customer experiences.
Choosing the right warehouse stock management system
Choosing the right Warehouse Stock Management System (WMS) is crucial for optimizing warehouse operations, improving accuracy, and increasing efficiency.
Types of warehouse management systems
Basic WMS
These systems handle fundamental operations such as inventory tracking, simple picking and packing processes and basic reporting. They are ideal for smaller operations or those with straightforward needs.
Advanced WMS
These offer more complex features like batch picking, cross-docking, labor management and detailed analytics. They are suitable for larger warehouses with more complex operations.
Integrated WMS
Often part of a larger enterprise resource planning (ERP) system, these are designed for companies needing a comprehensive solution that covers all aspects of business operations beyond just warehouse management.
Cloud-based WMS
These systems are hosted on the cloud, offering scalability, remote accessibility and lower upfront costs. They are becoming increasingly popular due to their ease of integration with other cloud-based applications.
Key features to look for in a WMS
- Real-time inventory tracking: essential for maintaining accurate stock levels and providing visibility across all channels
- Scalability: the system should grow with your business, accommodating increased volume without performance issues
- Integration capabilities: a good WMS should easily integrate with other systems such as accounting, customer relationship management (CRM) and purchasing software, as well as your POS
- User-friendly interface: ensures that your team can utilize the system effectively with minimal training
- Support and updates: look for a vendor that offers strong customer support and regular updates to keep the system secure and functional
Why Lightspeed is an excellent choice for your warehouse
Lightspeed offers a sophisticated yet user-friendly point of sale tailored to modern retail and wholesale demands. It works alongside your ERP system, like NetSuite, to help handle warehouse and front of house tasks.
Our strong focus on integration and real-time data processing sets us apart. Whether you’re operating a single warehouse or multiple distribution centers, Lightspeed’s POS seamlessly integrates with other business tools, providing a unified view of sales, inventory and customer data.
Lightspeed features a robust analytics tool that helps businesses forecast demand, optimize inventory levels and reduce waste. The cloud-based nature of Lightspeed ensures that it is scalable, cost-effective and always up-to-date with the latest features and security measures.
Bottom Line
Effective warehouse stock management is more than a logistical necessity—it’s integral to your business’s success, directly impacting everything from financial health to customer satisfaction.
By implementing a robust warehouse stock management system, you convert potential challenges into opportunities for growth, reliability and customer loyalty.
Whether you’re managing a sprawling furniture warehouse or a high-volume electronics distribution center, the insights and practices shared here can guide you towards more streamlined, efficient and error-free operations. And Lightspeed’s inventory management software could be the missing piece to bring it all together—why not watch a demo and see what we’re all about?
Frequently asked questions about warehouse management
What is a warehouse management process?
A warehouse management process encompasses the various strategies and methods employed to run warehouse operations smoothly and efficiently. This includes handling all aspects of the warehouse’s functionality from the time goods or materials enter the warehouse until they are moved out.
The process involves:
- Managing physical warehouse infrastructure
- Handling inventory, both receiving and packing
- Ensuring the correct processing and fulfillment of orders
- Overseeing workforce management
- Optimizing layouts and processes for storage and retrieval efficiency
- Implementing technology solutions like Warehouse Management Systems (WMS) to streamline operations
Effective warehouse management aims to minimize costs and operational delays while maximizing productivity and accuracy in order fulfillment.
What are the basic warehouse operations?
Basic warehouse operations refer to the foundational tasks required to manage the storage and movement of goods within a warehouse setting effectively. These operations typically include:
- Receiving: the process of accepting and checking shipments as they arrive, ensuring the goods match the purchase orders, and are free from damage
- Putaway: after goods are received, they are moved to their specific storage locations. Efficient putaway processes help in maintaining order and ease of access in the warehouse
- Storage: the safekeeping of goods in an organized manner to facilitate easy access and efficient space utilization. Proper storage prevents damage and loss of products
- Picking: the retrieval of goods from their storage locations in response to specific customer orders. This step is critical as it directly affects order accuracy
- Packing: packaging items appropriately once picked to prepare them for shipment to ensure they reach customers in good condition
- Shipping: dispatching of the packed items to the customer, including arranging for transport and documentation necessary for the goods’ delivery
- Inventory control: ongoing management of inventory to ensure that stock levels are maintained at sufficient levels to meet customer demand without overstocking
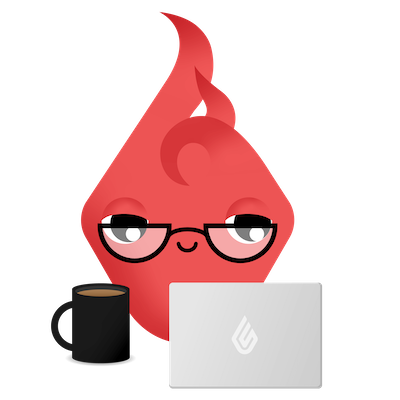
News you care about. Tips you can use.
Everything your business needs to grow, delivered straight to your inbox.