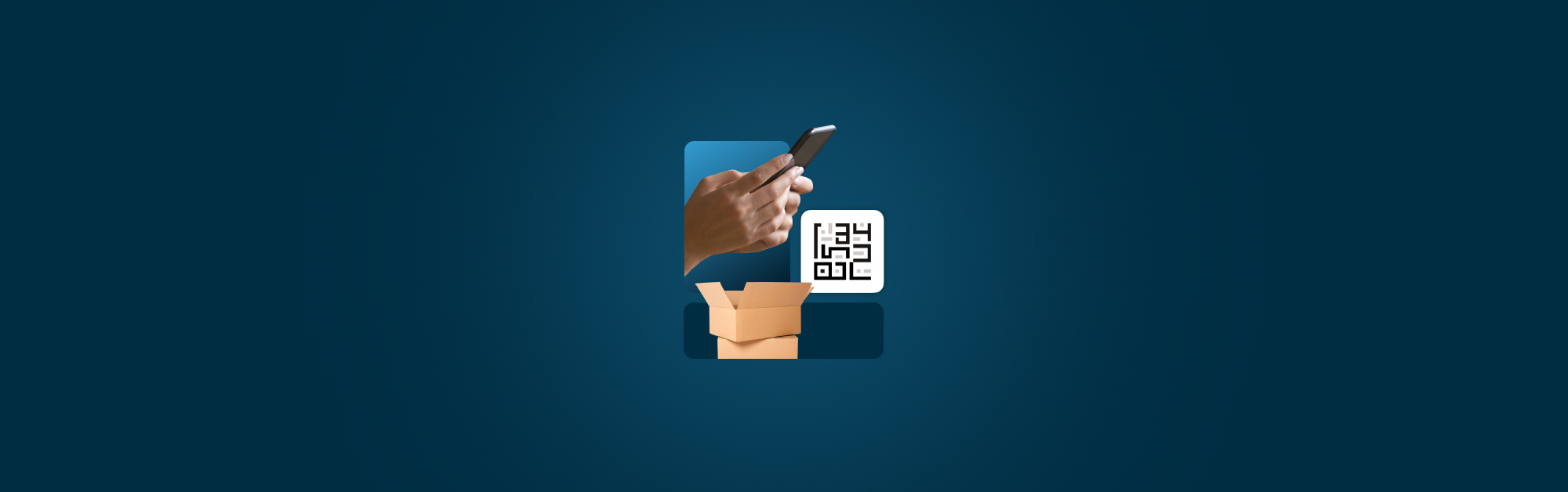
QR codes are transforming inventory management by providing a fast and versatile way to track and manage stock. These scannable squares can be attached to individual items or shelves, holding detailed product information such as serial numbers, location and purchase history.
Using a smartphone or dedicated scanner, businesses can instantly access this information, streamlining tasks like stocktaking, receiving goods and identifying items for sale or transfer.
Switching from barcodes to QR codes—or even just using them together—is easier than you might think. In this blog, we’ll go over what you need to know about QR codes in retail:
- QR codes vs. barcodes
- Why use QR codes for inventory management?
- Benefits of using QR codes for inventory
- How Lightspeed helps with implementing QR codes
Inventory Spreadsheet Template
Download this free inventory spreadsheet to help you better manage your stock, purchases and sales.
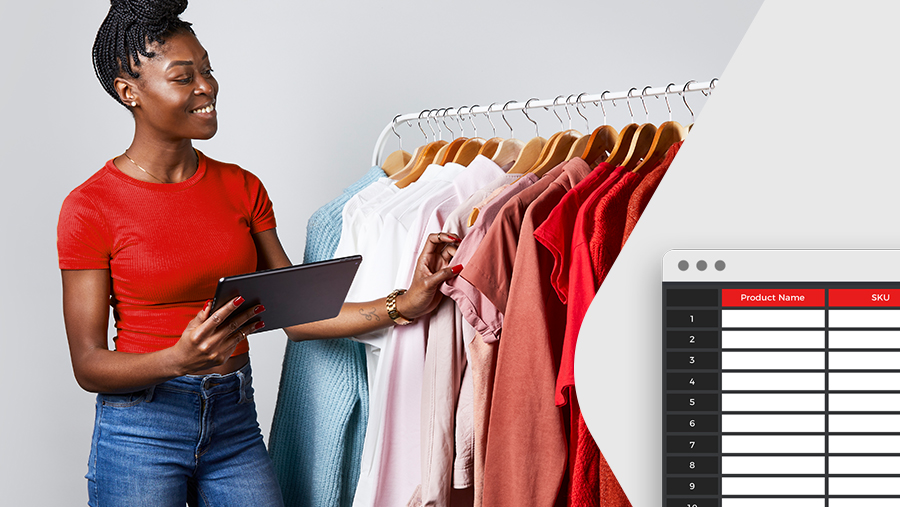
QR codes vs. barcodes
Both QR codes and barcodes are used to store and retrieve product information, but they differ in structure, storage capacity, and functionality.
- Barcodes are one-dimensional (1D) and typically store numeric data, which is read by scanning the code horizontally
- QR codes are two-dimensional (2D) and store much more information, including text, URLs and binary data, which can be scanned in multiple directions
This makes QR codes more versatile than traditional barcodes, as they can hold detailed product information, including inventory levels, expiration dates and supplier details, all in a compact, scannable format.
A comparison: functions of barcodes vs. QR codes
Feature | Barcode | QR code |
Data storage capacity | Limited to numeric or alphanumeric data (up to ~20 characters) | Can store significantly more data, including text, URLs and binary data |
Error tolerance and durability | Requires a clear and undamaged surface for scanning | Includes error correction, can be scanned even if partially damaged |
Scanning equipment | Requires specialized scanners | Can be scanned with a wider range of devices, including smartphones and tablets |
Integration with digital systems | Often requires additional software and hardware for advanced functionality | Integrates more seamlessly with digital systems, enabling actions directly from the scan |
Why use QR codes for inventory management?
Because of their 2D nature, QR codes are a level up. Here’s what you can do with them.
Real-time asset tracking
QR codes enable instant updates as items move throughout your supply chain. Scan a code upon receiving, stocking, transferring or selling an item, and your inventory system updates in real-time, ensuring accuracy and preventing discrepancies.
Monitoring inventory tracking details
Each QR code can store a wealth of information beyond just an item’s name. Track details like serial numbers, purchase dates, supplier information and even warranty details, all accessible with a quick scan.
Pros of QR codes for inventory tracking
- Comprehensive data storage: QR codes can store detailed information
- Real-time updates: scanning QR codes instantly updates inventory systems
- Error correction: QR codes include error correction features, allowing them to remain scannable even if partially damaged
- Versatile applications: QR codes can used across different inventory tasks, including tracking shipments, monitoring stock levels and managing returns
- Accessibility: QR codes can be scanned using widely available devices like smartphones
Customization for types of products
QR codes can be customized to suit different product types and inventory needs.
For example, a QR code on a piece of apparel might link to size and color variations, while a code on a piece of furniture might include assembly instructions or care guidelines.
Compatibility with UPC barcodes
QR codes can complement or even replace traditional UPC barcodes. This allows businesses to leverage existing barcode scanning infrastructure while taking advantage of the increased data capacity and functionality of QR codes.
Here’s how that might work:
- A product is labeled with both a UPC barcode for basic identification and a QR code containing more detailed information.
- At checkout, the cashier scans the UPC barcode as usual to identify the product and ring up the sale in the POS system.
- The QR code is scanned separately using a smartphone or tablet. This pulls up detailed information about the item, such as its current stock level, location in the warehouse or supplier details, which can be used for inventory management purposes.
- The QR code can also be used to provide customers with additional information, such as product specifications, user manuals or promotional offers, enhancing their shopping experience.
Seamless integration with existing inventory systems
QR code technology can integrate with your current inventory management software. This allows you to enhance your existing system with the benefits of QR codes without needing a complete overhaul.
Editing with dynamic QR codes
Unlike static QR codes, dynamic QR codes can be edited even after they’ve been printed. This allows you to update product information, redirect links or even change the destination URL as needed, providing flexibility and efficiency in your inventory management.
Static QR code | Dynamic QR code | |
Content | Fixed, embedded directly into the code | Editable, linked to a URL that can be updated |
Flexibility | Cannot be changed once created | Can be updated as needed without reprinting the code |
Tracking | No tracking data available | Provides scan data (location, time, device) |
Cost | Generally free to generate | Usually requires a paid subscription |
Best Use Cases | One-time use cases, simple information (e.g., WiFi password, contact details) | Marketing campaigns, evolving information (e.g., menus, event details, promotions) |
Example | Sharing your store’s Wi-Fi password | Linking to a landing page with a limited-time offer |
Benefits of using QR codes for inventory
Switching to QR codes for inventory management—or just integrating them into your existing workflow—could benefit your business greatly.
Ease of use
QR codes simplify inventory management by providing a quick and user-friendly way to access and update inventory information.
Unlike barcodes, which often require specialized scanners, QR codes can be scanned with smartphones, tablets or other common devices. This accessibility enables employees to update inventory, check product details, or verify stock levels on the go, improving operational efficiency. The ability to scan QR codes from various angles without the need for precise alignment further speeds up processes, reducing errors and saving time.
Optimal data storage
One of the most significant benefits of QR codes is their ability to store a large amount of data. While traditional barcodes can store only limited numeric or alphanumeric information, QR codes can embed detailed data far beyond that.
This eliminates the need to connect to an external database for every scan, streamlining inventory checks. By having essential data readily available within the code, QR codes enhance efficiency and reduce reliance on additional systems.
Size and versatility
Barcodes have standard sizes and aren’t very flexible. QR codes are compact and can be printed in various sizes to suit different needs. Their two-dimensional structure means they take up less space compared to traditional barcodes while providing more functionality. They can be affixed to items of all shapes and sizes, from individual products to pallets or storage bins.
QR codes are also versatile in their application, allowing businesses to use them for inventory tracking, quality control, shipment verification and more. Their adaptability ensures they fit seamlessly into diverse inventory processes.
Data security
QR codes can include encryption and error correction to protect the integrity of the data they carry. This feature ensures that even if the code is partially damaged, the information remains accessible and accurate.
Additionally, businesses can use encrypted QR codes to restrict access to sensitive data, ensuring only authorized personnel can retrieve it. This added layer of security helps increase accountability by tracking who scanned the code and when, enabling better oversight and traceability in inventory management processes. By their 1D nature, barcodes can’t offer that much security.
How Lightspeed helps with implementing QR codes
Lightspeed, combined with the strategic use of QR codes, empowers businesses to elevate their inventory management and operational efficiency.
Let’s go over how it could look to use Lightspeed Retail POS and QR codes in your business.
- Streamlined receiving and stocking: when new inventory arrives, staff can simply scan QR codes on items using their Lightspeed Retail POS app, instantly updating stock levels and product information in the system
- Effortless stock checks and transfers: With QR codes attached to shelves or individual items, staff can quickly scan multiple items to perform stock checks or initiate transfers between locations. Lightspeed Retail POS automatically updates inventory counts across all stores, ensuring accuracy and real-time visibility
- Enhanced product information: QR codes can store a wealth of information beyond basic product details, like supplier information, purchase dates, serial numbers and even warranty details with a quick scan. This provides staff with instant access to comprehensive product information, improving customer service and facilitating returns or exchanges
- Simplified customer interactions: QR codes can be used in stores to provide customers with access to detailed product information, reviews or even special offers. This empowers customers to make informed purchasing decisions and enhances their overall shopping experience
- Optimized inventory control: by integrating QR code data with Lightspeed Retail POS’s reporting and analytics features, businesses gain valuable insights into inventory turnover, popular products, and potential stockouts. This data-driven approach allows for informed purchasing decisions, optimized stock levels, and improved profitability
QR Codes in restaurant ordering with Lightspeed
Beyond retail, QR codes have become increasingly popular in restaurants. Customers can scan a QR code at their table to access the menu, place orders and even pay their bill. This reduces wait times, minimizes staff contact and provides a convenient and contactless ordering experience.
Lightspeed Restaurant POS integrates seamlessly with QR code ordering systems, streamlining operations and improving efficiency for restaurants of all sizes.
QR codes can take your business to the next level
QR codes are revolutionizing inventory management by offering a versatile, efficient and data-rich solution for tracking and managing stock. By embracing this technology, retailers can streamline operations, improve accuracy and potentially enhance customer experiences.
On the hunt for inventory management tools that make an impact? QR codes are a start. Lightspeed POS’ enhanced inventory management suite is the next step—watch a demo to see what we do.
Frequently asked questions about QR code inventory management
What is the main advantage of QR codes?
The main advantage of QR codes is their ability to store and share large amounts of data efficiently. Unlike barcodes, which are limited to numeric or simple alphanumeric information, QR codes can embed detailed information such as product descriptions, URLs and batch numbers.
Additionally, QR codes are scannable from any angle using common devices like smartphones, making them accessible and versatile for a variety of applications, including inventory, marketing and logistics.
Can QR codes be used for inventory management?
Yes, QR codes are highly effective for inventory management.
QR codes:
- enable real-time tracking of stock levels
- embed detailed product information
- allow easy scanning with smartphones or tablets
- improve efficiency by reducing reliance on external databases
QR codes can support automated workflows, such as triggering reorder alerts or updating inventory records, making them an essential tool for modern, streamlined inventory systems.
What are the benefits of QR codes in logistics?
In logistics, QR codes improve efficiency by providing quick access to detailed shipment information, tracking statuses and product details. Their high data capacity allows embedding of essential information directly in the code, reducing dependency on external systems. QR codes enhance accuracy in package handling, enable real-time tracking and improve accountability by recording scan history.
Why did QR codes replace barcodes?
QR codes have replaced barcodes in many applications due to their superior data capacity and versatility.
While barcodes are limited to numeric data, QR codes can store extensive information, such as URLs and product details, in a compact format. They can be scanned from any angle using common devices like smartphones, making them more convenient. QR codes also include error correction capabilities, ensuring they remain scannable even when partially damaged, providing greater reliability than barcodes.
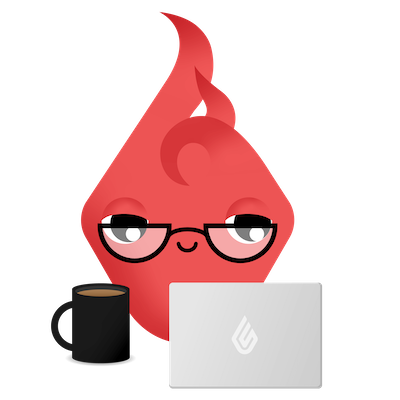
News you care about. Tips you can use.
Everything your business needs to grow, delivered straight to your inbox.