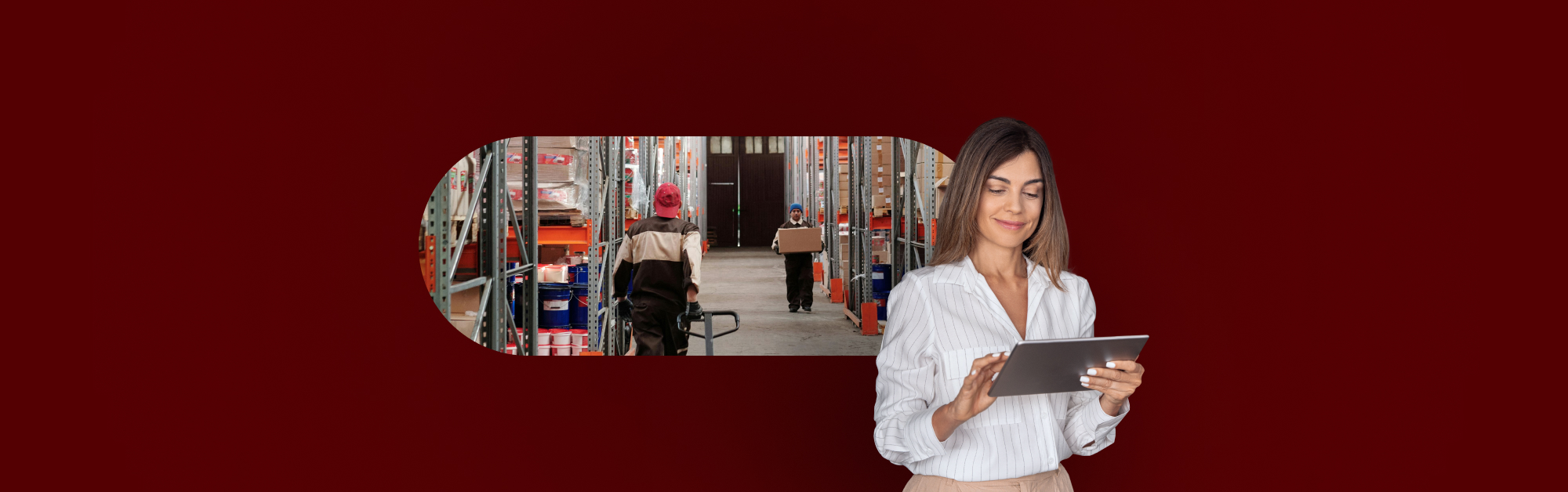
Having great products is a must for retail, but they won’t reach their full potential if your warehouse and inventory management processes are holding you back.
Separate and unconnected systems often cause bottlenecks, delays in fulfilling orders anddiscrepancies in stock levels. A unified approach towarehouse and inventory management software removes inefficiencies and provides immediate, accurate insights into stock availability.
When the right systems work together, businesses improve workflows, lower expenses and scale more effectively. Let’s break down how integration transforms operations, starting with inventory management.
- What is inventory management?
- What is warehouse management?
- Challenges of disconnected systems in business
- Benefits of integrating inventory and warehouse management systems
- Steps to successfully integrate warehouse and inventory software
Grow your retail business.
Streamline inventory, suppliers, teams and stores with Lightspeed's all-in-one platform. From intuitive POS and stock management features to powerful reporting, Lightspeed gives you the tools you need to grow.
What is inventory management?
Inventory management involves monitoring, controlling and optimizing stock levels to meet customer demand without unnecessary costs. For retailers, this means tracking products across all locations, predicting demand trends and reordering in time to avoid running out of stock oroverstocking items. The goal is to maintain enough inventory to support operations without tying up working capital.
Core tasks in inventory management include:
- keeping accurate records of stock quantities
- organizing items by size, location or other attributes
- using sales data to guide purchasing decisions.
Advanced inventory systems take this process further by automating tasks like setting reorder points and analyzing sales trends. These features allow businesses to reduce manual errors and make informed decisions based on real-time data.
Inventory management software simplifies these processes. It connects with tools like POS systems to provide a single, unified view of stock across all sales channels. Automated updates and real-time tracking help businesses meet demand, improve forecasting and increase profitability.
What is warehouse management?
Warehouse management organizes, stores and moves inventory efficiently within a storage facility. It ensures goods are received, stored, picked, packed and shipped accurately and on time.
Think of it this way: if inventory management tracks what you have and where it is, warehouse management ensures it gets where it needs to go efficiently and on time.
The process includes several key functions, specifically:
- Inventory storage, which involves categorizing and placing items for easy retrieval.
- Order picking focuses on selecting the correct products for customer orders.
- Order packing prepares goods for safe transit, while shipping coordinates the movement of outgoing orders to their destinations.
Each step works together, requiring accuracy and coordination to meet customer expectations.
A warehouse management system (WMS) supports this process by automating tasks like order tracking, stock location and shipping schedules. This reduces the time spent on manual work. Advanced systems often integrate with tools such as barcoding and RFID (Radio Frequency Identification), which ensure accurate stock counts and provide real-time updates. Centralizing this data gives businesses a clear view of their operations, enabling quicker and more informed decisions.
Strong warehouse management practices help maintain a smooth supply chain. They improve order accuracy, speed up deliveries and enhance overall customer satisfaction. With the right systems in place, retailers can cut costs and keep full control over their inventory.
Challenges of disconnected systems in business
Disconnected systems cause more than logistical problems—they disrupt the entire operation. For example, when inventory and warehouse management systems don’t talk to each other, retailers often end up with inaccurate stock levels. This disconnect can result in overselling products that aren’t available or missing sales opportunities by understocking popular items.
Another issue? Errors in order processing. When systems are separate, staff must manually transfer data between platforms, which increases the chances of mistakes and delays. A delayed or incorrect order isn’t just a hassle for your customers; it can harm your brand’s reputation, particularly in industries like retail or ecommerce, where speed and accuracy are critical.
Operating costs also increase when systems aren’t synchronized. Without real-time updates, employees spend unnecessary time fixing errors, manually checking inventory or tracking down misplaced stock. These inefficiencies waste resources that could be better used to scale the business or improve customer experiences.
Disconnected systems also make it harder to spot trends or optimize business performance. For instance, without unified data, you might miss recurring stock shortages at specific locations or fail to notice longer shipping times from certain warehouses. These blind spots limit your ability to address inefficiencies before they become bigger problems.
These issues compound and become serious hurdles for growing (and already large) retailers. Fragmented systems slow down response times and restrict growth. To stay ahead, businesses need integrated solutions that eliminate bottlenecks, reduce errors and ensure every part of the operation works smoothly together.
Benefits of integrating inventory and warehouse management systems
As you can imagine, connecting your inventory software and WMS can open up savings, efficiencies and opportunities in your business. Consider the following.
Streamlined operations
Combining inventory and warehouse management systems connects stock tracking with physical storage operations. Real-time data updates ensure inventory levels stay accurate by instantly reflecting sales, returns and incoming shipments. This removes the need for manual data entry, which often causes errors and delays.
More accurate inventory tracking
Integration leads to precise stock tracking. When inventory systems communicate with warehouse operations, businesses gain full visibility into what’s in stock, what’s incoming and what needs replenishing. This reduces the risk of overselling items or overstocking, allowing you to meet customer demand while avoiding excess inventory costs.
Smoother order fulfillment
Order fulfillment becomes quicker and more dependable. Integrated systems automate workflows for picking, packing and shipping, minimizing errors and delays. For instance, when an order is placed, the system immediately alerts the warehouse to begin processing. This reduces turnaround times and ensures faster deliveries.
Lower costs
Operational costs decrease with streamlined processes. Automation reduces the need for manual tasks like updating stock, processing orders and reordering. Integrated systems also provide insights into warehouse space usage, helping businesses use storage areas more efficiently.
Smarter forecasting
Demand forecasting improves when inventory and warehouse data are combined. With access to trends and patterns, businesses can predict future needs more accurately. This prevents overstocking slow-moving products and ensures sufficient supply of high-demand items.
Happier customers
Customer satisfaction increases with accurate and timely deliveries. Aligned systems ensure orders are processed correctly and shipped on time. Real-time tracking adds transparency, allowing customers to follow their orders from placement to delivery.
Better visibility into your business
A single dashboard gives managers a clear view of inventory and warehouse operations. Stock levels, order statuses and warehouse performance are all visible in real time. This centralization simplifies decision-making and helps businesses respond quickly to any challenges.
All this to say that integrating your inventory and WMS is more than a technical update—it’s a strategic improvement that strengthens operations across the board. So if you haven’t done so yet, start integrating these systems ASAP.
Steps to successfully integrate warehouse and inventory software
Assess current systems and identify integration needs
Start by reviewing how your current systems perform and where they fall short. Identify bottlenecks and inefficiencies that slow down your business operations.
For example, separate stock tracking and warehouse workflows can create information gaps and prevent real-time updates.
Focus on the specific challenges your business faces. A retailer with multiple locations might prioritize centralized inventory tracking, while an ecommerce business may need faster order fulfillment.
For best results, set clear goals for the integration process. This can include setting objectives like: reducing stock errors, automating tasks or improving synchronization across systems.
Choose the right software solutions
Not all software will meet your needs. Look for platforms that not only address your current requirements but also have the scalability to grow with your business. Prioritize systems that integrate seamlessly with your existing tools, such as POS platforms or supply chain management software.
Key features to look for include real-time stock updates, warehouse automation and detailed reporting capabilities. Make sure the software supports important integrations, like barcoding tools or shipping platforms, and confirm it works with your current hardware setup.
Plan the integration process
Create a timeline with clear milestones to manage expectations and allocate resources effectively. Factor in costs for software, IT support and potential hardware upgrades.
Assign specific roles to your team, from IT staff to warehouse employees, so everyone knows their responsibilities. Roll out the integration in stages starting with a smaller pilot program to test the system before implementing it across all locations.
Train staff and secure stakeholder buy-in
The success of your integration depends on your team. Provide thorough training to help employees understand how to use the new workflows and tools. Go beyond technical training by showing how the system improves their daily tasks and streamlines operations.
Get leadership and stakeholders involved early. Explain how the integration saves time and increases efficiency. Their support helps build confidence among team members and fosters a sense of shared commitment to the new system.
Test and monitor the integrated system
Before fully launching the new system, conduct extensive testing. Simulate real-world scenarios like order processing and stock updates to identify potential issues. Pay attention to data system speed and compatibility with third-party tools.
Once the system is live, track its performance through metrics like order accuracy, processing times and stock discrepancies. Use analytics to find areas for improvement and adjust as needed. Regular updates and feedback from your team will keep the system running smoothly as your business grows.
Bottom Line
Integrating inventory and WMS is essential for growing businesses in competitive markets. By uniting these core functions, businesses eliminate inefficiencies, improve accuracy and scale operations seamlessly. Integration simplifies workflows, reduces errors and ensures real-time data synchronizes across locations, leading to faster, more reliable order fulfillment and better customer satisfaction.
Disconnected systems, in contrast, create costly bottlenecks and missed opportunities. Synchronizing inventory and warehouse management not only resolves these challenges but also provides actionable insights for better decision-making. For businesses managing multiple locations or large inventories, integration is critical to unlocking operational efficiency and long-term growth.
Talk to an expert to learn how Lightspeed can help grow your business and create the streamlined processes you need to succeed.
FAQs
What is the difference between inventory management and warehouse management?
Inventory management tracks and controls stock levels across sales channels and locations to ensure products are available when customers need them. Warehouse management oversees the physical storage, movement and handling of goods within a facility to make the best use of space and streamline operations. While inventory management focuses on keeping stock accurate, warehouse management ensures orders are fulfilled efficiently. Combining both systems creates a more seamless supply chain process.
How does integration help with inventory forecasting and demand planning?
Integration connects real-time sales data, stock levels and warehouse operations, giving businesses accurate insights for forecasting. Centralizing this information helps businesses spot trends, predict demand and automate reorders to prevent stockouts or excess inventory. This leads to better planning, less waste and stronger profitability, all supported by reliable data.
What are the common challenges in integrating inventory and warehouse management systems?
Integration often runs into hurdles like data silos, where systems don’t communicate properly, causing delays and errors. Outdated software or hardware may also lack compatibility, requiring upgrades or additional tools to bridge the gap. On top of that, training employees on new workflows and minimizing disruptions during the transition are key challenges businesses need to tackle for successful implementation.
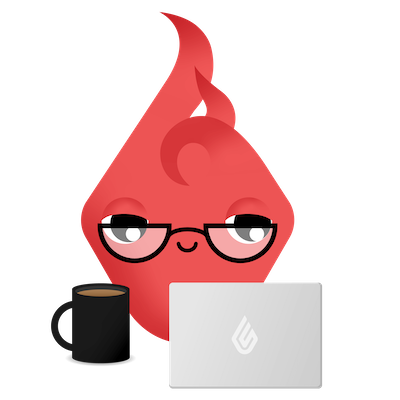
News you care about. Tips you can use.
Everything your business needs to grow, delivered straight to your inbox.