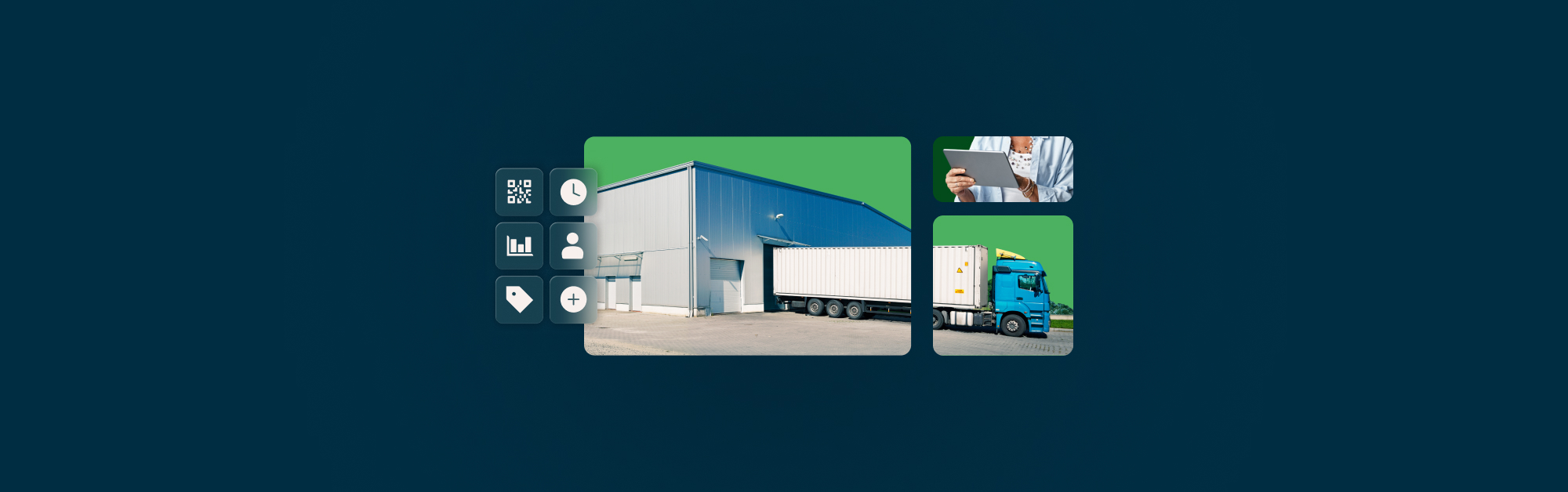
Managing a retail warehouse is no small task. Challenges like maintaining accurate inventory levels, optimizing storage and ensuring timely order fulfillment can disrupt your operations and hurt your profits if not handled effectively.
Warehouse management software helps address these challenges. It offers tools to streamline processes, boost accuracy and scale operations as your business grows. With the right features in place, warehouse operations become faster, more efficient, and less prone to errors.
In short, you gain control and set your business up for scalable growth.
And growing retailers, the right tools aren’t a luxury—they’re a requirement to keep up with competitors and meet customer expectations. Below, we’ll break down the features that define a solid warehouse management system.
- What are the key features of warehouse management systems?
- Lightspeed POS: a comprehensive solution
- Choosing the Right WMS
Grow your retail business.
Streamline inventory, suppliers, teams and stores with Lightspeed's all-in-one platform. From intuitive POS and stock management features to powerful reporting, Lightspeed gives you the tools you need to grow.
What are the key features of warehouse management systems?
Inventory tracking and control
Real-time visibility into inventory ensures stock levels remain accurate. A well-designed WMS updates inventory movements instantly, preventing stockouts andoverstocking. Features like SKU tracking and automated alerts help maintain control and support preciseinventory management.
Receiving and put-away
A WMS simplifies receiving by logging incoming shipments directly into the system. It also directs staff on where to store items for optimal efficiency. This reduces mistakes, speeds up the put-away process, and ensures inventory is easy to locate when needed.
Order picking and packing
Order fulfillment relies on efficient picking processes. Methods like batch picking, zone picking and wave picking reduce the time required to locate products while improving accuracy. Packing tools further enhance the process by ensuring orders are correctly prepared for shipping.
Shipping
A reliable WMS streamlines shipping by generating labels, tracking packages and managing delivery schedules. This ensures timely shipments that leave customers satisfied. Carrier integration also saves time and ensures smooth delivery management.
Labor management
A WMS optimizes productivity by assigning tasks, monitoring staff performance and offering insights for better resource allocation. These tools ensure that employees are efficiently scheduled and positioned to meet operational demands.
Yard management
Warehouses handling large volumes benefit from tools for managing trailer movements and gate operations. A WMS tracks check-ins and controls yard flow, reducing delays and keeping operations smooth from arrival to departure.
Barcode scanning and RFID integration
Barcode and RFID technology brings speed and accuracy to inventory tracking. By scanning items into the system, errors from manual entry are eliminated, and processing times improve. This results in faster order fulfillment and updated inventory records.
Space optimization
WMS tools analyze storage needs and create layouts that minimize unnecessary movement within the warehouse. Efficient use of space increases storage capacity and improves operational flow.
Batch and serial number tracking
Tracking batch and serial numbers is vital for meeting regulatory requirements and maintaining quality control. This feature supports perishable goods management and ensures traceability throughout the supply chain.
Reporting and analytics
Detailed reporting tools offer insights into KPIs likeinventory turnover, order accuracy, and warehouse productivity. These analytics guide better decision-making and help identify areas needing improvement.
Integration capabilities
A strong WMS connects seamlessly with systems likepoint-of-sale platforms, e-commerce solutions, and enterprise resource planning tools. These integrations create a unified flow of data and streamline operations across your supply chain.
Multi-warehouse management
For businesses spanningmultiple locations, centralized inventory management is key. A WMS provides tools to monitor stock levels and maintain consistency across all warehouses and stores.
Cross-docking
Cross-docking features reduce storage costs by moving products straight from receiving to shipping. This minimizes handling time and speeds up the fulfillment process.
Returns management
Streamlined returns handling bolsters customer trust and minimizes losses. A WMS updates inventory immediately and tracks returned items, making the return process simpler and more efficient.
Safety and security features
Secure access controls and tools for handling hazardous materials ensure warehouse safety. Compliance with safety regulations protects both employees and stored goods.
Mobile capabilities
Mobile access enables managers and staff to update the WMS and stay connected from anywhere. This flexibility keeps operations running efficiently and allows real-time adjustments.
Lightspeed POS: a comprehensive solution
A strongpoint-of-sale system does more than handle transactions. When paired with warehouse management features, it becomes a central hub to simplify operations and improve efficiency throughout your retail business. By integrating inventory tracking, order management, and detailed analytics, it brings together every part of your retail and warehouse processes.
Key features for retail warehouses
- Real-time inventory tracking: Keep an accurate view of stock levels as they change, even across multiple locations. This reduces the risk of stockouts and prevents overstocking, keeping your inventory organized and efficient.
- Automated reordering: Use reorder points to automatically generate purchase orders when stock reaches a certain level. This automation saves time and ensures shelves are consistently stocked with the right products.
- Advanced reporting tools: Access in-depth reports on sales patterns, inventory turnover, and warehouse performance. These insights help you make smarter decisions and pinpoint areas that need improvement.
Why it stands out
Lightspeed POS integrates effortlessly with other retail tools, creating a single platform to manage your operations. It simplifies tasks like multi-location inventory management and provides the adaptability needed as your business grows. With features designed to reduce manual mistakes and enhance accuracy, it supports your warehouse and retail operations seamlessly.
Features like barcode scanning and batch tracking ensure accuracy from receiving stock to shipping orders. Centralizing data and accessing it in real time allows retail managers to make quick, informed decisions. For businesses managing multiple warehouses or stores, the system promotes consistency and clear communication across all locations.
Choosing the Right WMS
Choosing a warehouse management system goes beyond simply checking off a list of features. It’s about finding software that aligns with your business’s specific operational needs. Start by focusing on tools that improve efficiency, such as real-time inventory tracking, order picking methods, and seamless integration with other systems you already use. A centralized system that syncs data across platforms leads to smoother workflows and fewer mistakes.
Scalability is key for retailers who are growing or managing multiple locations. Features like multi-warehouse management and advanced analytics help ensure the system grows with your business. Automation tools, including barcode scanning, automated reordering, and cross-docking, simplify routine tasks and free up time for your team to focus on higher-value activities.
Security and mobility are just as important. Systems with strong access controls protect sensitive business data, while mobile capabilities keep managers and staff connected and informed, no matter where they are. Focusing on these features ensures your WMS not only meets your current needs but also supports your long-term growth plans.
Conclusion
For growing retailers, optimizing warehouse operations is critical to maintaining a competitive edge. A reliable warehouse management system ensures accuracy, streamlines processes, and integrates seamlessly with your existing tools. Features like real-time inventory tracking, advanced analytics, and automation simplify day-to-day operations, enabling you to focus on scaling your business effectively.
Lightspeed’s comprehensive POS system, combined with robust warehouse management tools, offers everything you need to efficiently manage inventory, fulfill orders, and support multi-location operations. Its adaptability and ease of use make it an ideal choice for businesses looking to grow while maintaining operational excellence.
Watch a demo to see how Lightspeed can transform your warehouse management and help take your business to the next level.
FAQs
What are the challenges in small business inventory management?
Holding too much stock can drain cash flow and increase storage expenses, while not having enough inventory leads to stockouts and lost sales opportunities. On top of that, relying on manual processes often creates errors, making it harder to keep records accurate and predict demand reliably.
What are the best practices for small business inventory management?
Accurate inventory management starts with using a system that updates stock levels in real time. Establish clear reorder points to avoid overstocking or stockouts, and conduct regularinventory audits to catch any inconsistencies early. Adding tools like barcode scanners orcloud-based inventory management software can also simplify operations and minimize mistakes caused by human error.
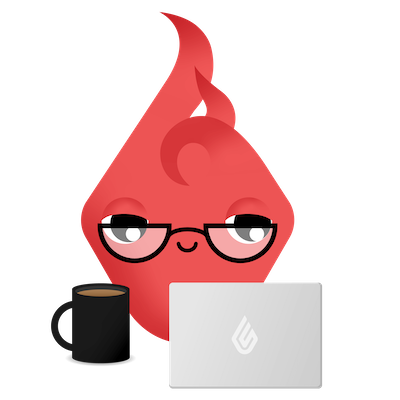
News you care about. Tips you can use.
Everything your business needs to grow, delivered straight to your inbox.